Fr. TADEUSZ CIBOROWSKI
WARSAW HIVE
WOODEN AND STRAW
TOGETHER WITH EQUIPMENT
34 drawings in the text
EDITION II
ŁOMŻA 1937
PRINCIPAL STOCK AT BOOKSTORE "UNITAS" IN ŁOMŻA
Fr. TADEUSZ CIBOROWSKI
WARSAW HIVE
WOODEN AND STRAW
TOGETHER WITH EQUIPMENT
34 drawings in the text
EDITION II
ŁOMŻA 1937
PRINCIPAL STOCK AT BOOKSTORE "UNITAS" IN ŁOMŻA
All rights reserved.
Diocesan Printing House
in Łomża.
PREFACE TO THE SECOND EDITION.
The first edition, entitled "Warsaw Hive its construction and equipment", sold five thousand copies in a relatively short time. As a copy of "Work in the Apiary" it was extremely cheap, hardly calculable in the book trade. Now, having exhausted the print run, I am beginning the production of a separate booklet, taking into account small corrections in the text, and at the request of readers, adding a description of the construction of hives made from straw mats.
My views on the value of the Warsaw hive have not changed, as before, I consider this hive to be the best for our climatic conditions.
The Warsaw hive is the original Lewicki hive with an upright structure, having a narrow-high frame. It is known not only in our country but also throughout Russia; it was introduced there shortly after it was built by the inventor and several thousand copies were widely modelled.
This hive is popular because it successfully answers the demands from the bee colony, providing living conditions as close as possible to the nature of the swarm, and sufficiently protecting it from atmospheric influences. The original Lewicki hive could produce 50 to 80 kg of honey in nectar rich areas.
In Russia, this hive is being displaced by American hives thanks to beekeeping instructors trained in America, where the government sent many for a 3 year beekeeping apprenticeship. It was after the Japanese war. Instructors influenced by American practice began to introduce a new type of beehive, preventing the doubling of walls with the disadvantages of a cool design due to the predominantly harsh Russian climate.
In the Republic there is no need to renounce your Polish hive; it is the crown of inventive Polish thought in all its smallest details. This hive, equipped with a superstructure and deprived of superfluous legs by Brzóska, excels because it meets all the requirements of modern beekeeping.
In the meantime, the number of the latest hive inventions was joined by one more, which was given the name "Warsaw beehive widened". As the newest type, he has an avid following, slamming copies for his tall and fashionable qualities. The principle of the widened hive is the "stacked frame" from the American Dadant Blatt lounger. The frame of the extended hive measures 435 mm high, 300 mm wide, and the Dadana frame measures 300 mm high and 435 mm wide.
We know the principle that a hive is built for the frame, so if the "widened" hive is built for the American frame, it should be properly called: "American hive erected", which has nothing to do with the Warsaw Lewicki hive, because such a significant widening of the frame (60 mm) is far from the author's creative thought.
Has the "enlarged" hive turned out to be better in beekeeping practice than the Warsaw hive? I myself did not directly build or work in a new type of beehive, because it did not logically appeal to me, but I met beekeepers who, encouraged by advertising, built American beehives set up in the Warsaw skin. Several years of practice have proven that this beehive is not the best beehive, indeed it differs very much to its disadvantage from the real Warsaw beehive. The real value of a thing is judged after its contact with life: an American egg does not fit into a Polish nest.
So let's stick with the tried-and-tested Warsaw top hive, which has successfully passed a nearly 40-year trial. Yet it did not grow old, being at the same time a purely Polish invention without foreign admixture and unjustified accretions.
Author.
on November 18, 1936.
HIVE.
At the forefront of all technical issues in beekeeping is the design and construction of the hive. The beehive is a living honey factory. We understand perfectly well that although bees abandoned their natural habitat in hives and moved to artificial settlements, they did not lose their nature and natural requirements in their development and production. Just as it is a matter of science to slowly discover the laws governing the life of bees, so it is a matter of intelligent technology to create a framework for bee life, i.e. to build hives that would most closely correspond to the innate idea of the "dwelling" of bees.
The design and construction of the hive are not indifferent, indeed they are among the factors that will determine either the flourishing of beekeeping in the Republic of Poland in the future, or its bankruptcy in the area of international trade. Meanwhile, "in Poland, as you like." We have standing, lying, frame, bar, expandable and fixed beehives in use, we have straw of all types, species and sizes, the so-called skeps, baskets, straw mats, sewn, according to various possible and impossible ways, finally we have boxes of all names and professions, starting from the ordinary peasant one with frames made of kindling or offcuts, and ending with foreign lying and standing systems - in short, like a fair.
What is the best and most appropriate? Let's consider.
1. Conditions of a good hive. A hive is a man-made settlement for bees, where swarms can live, reproduce and lay honey. In order for the hive to fully respond to these living conditions, there is no doubt that it must be built with a complete knowledge of "Bees"*), that is, with an understanding of bee life and nature, and with an organizational sense of the trunk.
The history and the traditional way of building a nest and brood in the shape of an ellipsoid testify to the fact that the bees' natural habitat has been hives in a living tree since time immemorial. The case of the hive became vital from the moment when man moved swarms from beehives to boxes, and especially when he used movable frames for his convenience and began to deliberately work in the apiary.
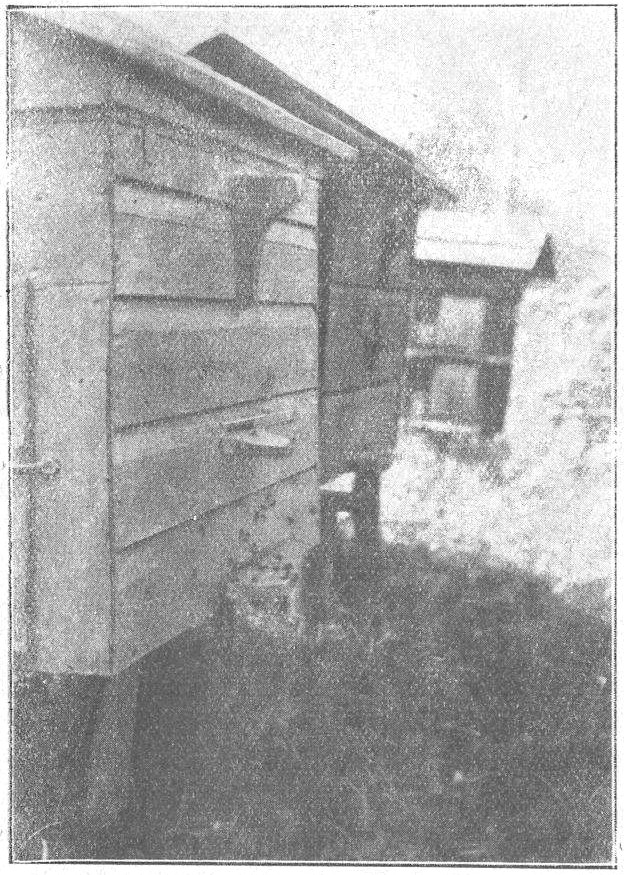
Dig. 1.
Warsaw palaces (own photo).
*) "Bees, or the science of bee life and nature" by the same author.
We will not dwell too much on the superiority of a demountable hive over a hive. This is an undeniable fact and has already been recognized by everyone, even very few progressive honey hunters.
Ciesielski defines the conditions of a good hive as follows: “A hive should be: — 1) cheap, 2) durable, 3) of the simplest construction possible, 4) light, 5) warm, 6) reasonably spacious, 7) comfortable for the bees and the beekeeper ". The incomparable Ciesielski is absolutely right: such conditions are necessary and clear.
Among the many types of hives used by us and corresponding to the above conditions, the so-called Warsaw Street, i.e. Lewicki Street, described here in its final form. Although this hive is not cheap or light, it is really difficult to concentrate all these features in one hive system so that it can fulfill its task with today's diverse beekeeping requirements. For example, if we want the hive to be sufficiently spacious, it must be large and therefore heavy. And it must be big if we want the bees strong from spring, not swarming through the summer, to be able to have enough space. The Warsaw hive, with its skilful use and swarm management, can satisfy the natural requirements of bees and turn out to be very practical in use. The high price of the hive is also a disadvantage in a difficult time in terms of pennies and credit, but for the poor beekeepers, properly built straw houses may be enough for the time being. With good intentions and skills, having a "straw" apiary, you can gradually cover more expenses for frame hives with the income from it and eventually get a "wooden" progressive apiary.
If every average beekeeper in Poland made only one proper box hive for his apiary every year, then after 15 years all our bees would live in "palaces
of Warsaw”.
From the point of view of the organization of beekeeping work in the entire Republic of Poland, to the calculated conditions for a good hive, one should also add the wish that the hives throughout our country should be of exactly the same dimensions. By this we would gain much for science, industry and commerce, because on the one hand, any improvement in beekeeping introduced somewhere far away by one beekeeper could easily be adopted everywhere without special expenditure, on the other hand, all commercial transactions could be carried out more easily with the greatest possible convenience and speed.
In addition to the Warsaw hive, the American hive, built by Dadant and improved by Blatt, commonly known as dadan, has become popular in Poland recently. He gained fame not because he is suitable for our national beekeeping establishments, but probably only because he is "American".
The famous Russian scientist Prof. Serbinov*), a researcher of the life of bees, especially the foulbrood, the author of many works on beekeeping, writes:
“Without doubt, the hive system plays a great part in the development of the European foulbrood in the form of its more or less malignancy. There is no doubt that the Northern Russian system of Dadant-Blatt hives does not quite match up. The large size of the hive does not keep enough heat, especially in cold summers, which I have often observed in peasants.
“Of all the hive systems from the point of view of combating foulbrood, the most suitable for the north, in my opinion, is the Lewicki hive.
“Anglo-American beehive, recommended even by a special commission of Ros. T-wa Pszczelniczy, as very convenient and profitable in bee-keeping, is not very rational when it comes to foulbrood in northern provinces. Yes, it is good in spring, it often gives early swarms, but in summer, due to the small volume of its nest, it is stuffy inside, especially in dry and hot years. I have witnessed many times that bee colonies strong from spring fell ill in this hive to a very vicious and persistent foulbrood of uncovered brood. In the north, this hive is the other extreme in opposition to the Dad.-Blatta hive. During the strong development of the trunk, it holds too little air in relation to the amount of the fly, and in the spring the maggot develops in it abundantly.
From Serbinov's quoted opinion, we can conclude that this eminent scientist is not only convinced of the superiority of our beehive over the above-mentioned ones, but he directly praises it as the golden mean. remedy to fight beekeeping blight — foulbrood. Needless to say, a hive that stands up to criticism and performs well in the most unfavorable conditions must be excellent and worth recommending also for use in normal conditions.
You praise others, you do not know your own...
Bees easily adapt to the conditions they will encounter in the estate provided to them. This circumstance causes illusory results when observed superficially. Let's take a look at the construction of the hive that is most suitable for us. Of course, in terms of detailed study, I give priority to the Warsaw hive.
*) J. L. Serbinow "Rotting bees and bor'ba with him." Petersburg 1910, p. 74.
2. Warsaw street. It is a box with a removable or movable roof, supported when opening on a suitable support, nailed to the front wall. When opened, the visor leans towards the eyelets so that you can work freely without disturbing the bees in the outlet. The bottom of the hive cannot be movable, because the tree, even the best, shrinks, warps and creates gaps, and thus drafts.
The inside of the hive is 252 mm wide, 750 mm long and 500 mm deep.
The basic dimensions in a hive are: the size of the frame and its distance from the walls, so the width of the frame is 240 mm and the distance on both sides is 6 mm. The location of the outlet is also important, it should be in the middle of the front wall at a distance of 250 mm from the ceiling, not more than 300 mm. Less important is the space under the frames, which is to be different in winter and different in summer, and the length of the hive's interior, as well as its construction that gives warmth, beautiful appearance and protection against leaking.
The nesting frame of the Warsaw top hive, outside width 240 mm, height 435 mm. Side and upper bars - 24 mm wide (one Polish inch), 8 mm thick, lower, called fringes, 8 by 10 mm. The fringes, connecting the sides of the frames, protrude beyond them on both sides by 4.5 mm. The side beams, 435 mm long, have a tenon height and width of 8 mm at their upper ends, and a groove at the bottom, like a groove (feder), through which the ends of the connecting lower beam, 8 by 10 mm, pass (Fig. 4 o, b).
The frame in the Warsaw hive hangs on the arms (whiskers) in the rebate (felc) 7 mm wide and 8 mm deep. The upper bar is to extend loosely to the end of the frame, so it is 264 mm long.
The bars are planed outside only, inside they remain rough with a cut (schnitem), so that the bees have the opportunity to make strong combs. No accessories inside the frame are needed, so the triangular slat is not nailed to the middle of the upper bar, the side bar is not rounded, it is not advisable to fasten the upper bar, which is needed only for frames in deckchair hives, due to the considerable length of the upper bar., Any additions inside the frame dimension, crossbars increasing the thickness of the bars, are unnecessary, because they only reduce the frame clearance and take up valuable space in the hive. (Fig. 2 and 3)
There are two holes in the upper bar (Fig. 4 c), 8 mm in diameter, 240 mm apart with their outer edges, i.e. the width of the frame; in this way, 12 mm arms are formed from its ends, on which the frame hangs in the frame (rabbet) of the hive. The ends of the sill protruding beyond the sides allow for a moderate distance between the side of the frame and the hive wall during its removal and prevent crushing of bees (Fig. 4b). The letters a in Figures 4, 6 and 7 mark the spacing nails, two on each side, protruding above the surface of the bar side by 12 mm, i.e. together with the bar, they form a 36 mm thick frame. The nails are without heads so that they do not interfere with the work on the honey extractor. They are driven into the side bar on the right side from the bottom and into the upper one on the left near the end. They can also be driven in opposite the hole, whereby the tenon of the side beam is fixed.
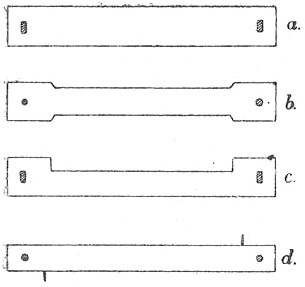
Dig. 2.
Different forms of the upper bar of the socket frame, a, Lewicki, b, a transitional form used for the superstructure, c, unacceptable, d, it should be (own drawing).
Closed frames must be rectangular and not tilted (twisted). For a more reliable preservation of an unchanging form, it is good to nail them on a rule arranged for this purpose (Fig. 5), on which staples should be nailed in appropriate places to the extent of the protrusion of the spacing nails. In the absence of a board, make a hardwood anvil with a cut in the center exactly 36 mm deep. Before driving the nail, it is good to puncture the bar with an awl to prevent splitting.
The sill, with its 8 mm thickness and 10 mm width, enters completely into the lower cut of the side beam (o in Fig. 4) and is attached to it with a nail about 30 mm long, which, when driven in part, protrudes 12 mm downwards. It is needed so that you can support the frame on the hive during work and not crush the bees hanging under it.
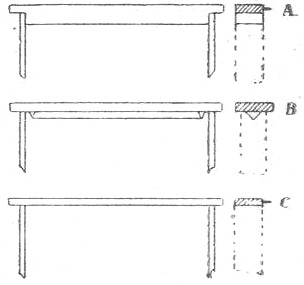
Dig. 3.
The upper bar of the socket frame seen from the side. And according to St. Brzósko, B, with a triangular slat nailed to it, C, should be in the hive stand (own drawing).
The hive is built for the frame. We make a box 252 mm wide inside, 500 mm deep, 750 mm long. The side walls have a rebate, carved along the entire length from the inside, 8 mm deep. and 7 mm wide, so the hive has a depth of 492 mm from the frame. The rebate serves as a bearing for the arms (whiskers) protruding beyond the side bar of the frames.
The bottom is immovable, made of half-track, nailed across and nailed to the lower edges of the walls and to the top.
The walls of the hive are of 36 mm (1.5 inch) boards, glued together with a feder, i.e. there are gaps in the edges of the fitted boards, into which the slats smeared with glue are killed. The top boards are made, similarly to the bottom, from half-tracks joined together by a groove, the same is the connection of the bottom.
The essential thing in the construction of a hive is to ensure that it does not change its internal dimensions and shape in width. It is therefore necessary to use dry wood so that there are no gaps, and the box is nailed around with the lengths of the boards, because the drying of the tree along the length is the least visible. Therefore, the bottom and tops are made of transverse boards.
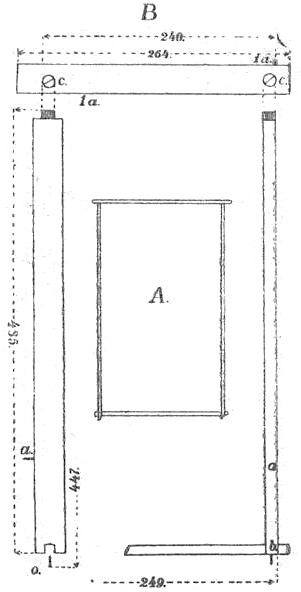
Dig. 4.
A. Warsaw frame in its entirety. B. frame components. Upper and left side bar - view from above on the plane (Fig. on). The numbers indicate dimensions in mm.
One gable is built-in, in the other we leave room for a door, called a valve. It is not important at which peak the valve should be, yes, in larger apiaries they should be given alternately, which sometimes makes it easier to place the hives closer on the toque or in the locker for the winter. The door opening has the inside width of a hive and a height of 370 mm. The door itself has the same but smaller dimensions; they are, if possible, made of a single piece of board, fitted with a rebate (anszlag), i.e. they close the hive exactly and with the outer edge protruding after closing, they cover the gaps. They move on hinges made of four staples and are fastened from the inside with a fin strip (floor) transverse. From the inside, they can be closed with a suitable cap (Fig. 12).
Both tops protrude beyond the surface of the hive box by 60 mm, and the bottom by 50 mm, thus forming wings to which the boarding is nailed (Fig. 6 e).
The superstructure is an oblong box made of 17 mm (3/4 **** inch) boards, without a bottom, with a rebate to the frames at the top in its side walls. Placed on the hive, on the nest box - it corresponds with half the thickness of its boards to the ends of the tendrils of the nest frames; the remaining half of the thickness extends above the box-and-a-half box. Placed in this way, it raises the hive up on one line of its inner walls.
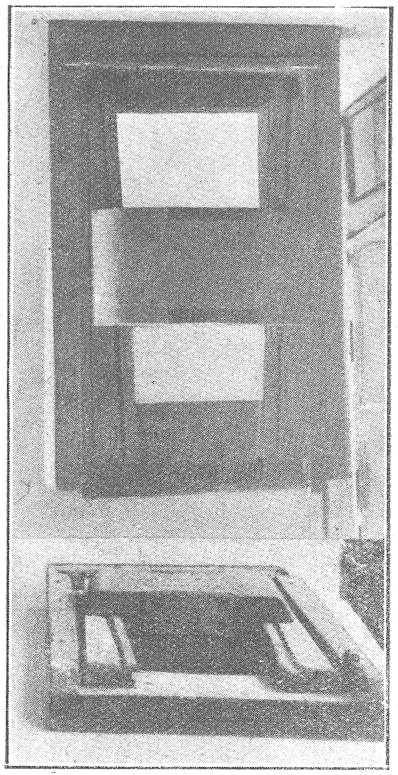
Dig. 5.
The rule for nailing frames. Above - front view, below - view from the lower gable (own photo).
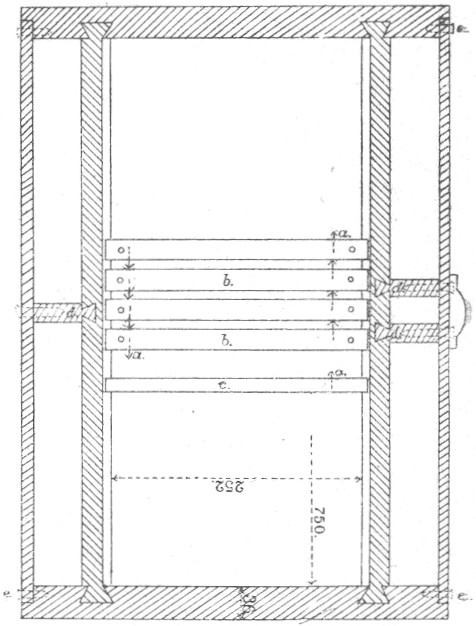
Dig. 6.
Horizontal projection of the Warsaw hive where the nest frames are hung, a spacing nails, b frames, c gate d vertical slats, e ribs at the ends. gables for nailing the formwork (own drawing).
The width of the extension inside is the same as that of the hive - 252 mm, with the same. as in a beehive, with a rebate 7 mm wide, but 5 mm deeper, so 13 mm deep. It is used to hang overhead frames, 158 mm high. The extension inside is 152 mm from the frame, and the extension frame, not counting the upper beam, is 150 mm (158-8=150), so it is 2 mm higher than the frame, intended for drying of the board.
The extension does not stand directly on the socket, but on short posts, 5 mm high (Fig. 7, No. 5). These posts, fixed with nails on the top of the nest box, in places corresponding to the corners of the superstructure, are used to create the necessary distance between the nest and the superstructure and allow it to be positioned without the fear of crushing the bees.
Bearing for the extension. In order for the superstructure to fit under the roof of the hive, a sufficiently high headboard should be arranged for it, built 80 mm above the top of the nest frames, into which it should enter quite tightly so that it does not leave gaps on the sides, where pests could multiply and where bees could crawl out under peak.
The bearing is created in such a way that the tops of the hive protrude above the level of the nest by 80 mm and the side boards corresponding to the sides of the superstructure are nailed to them. The placenta is 288 mm wide and as long as possible longer than the inside of the hive; therefore, it is necessary to give the gable boards opposite the tops of the superstructure not half-track boards (36 mm), but square ones (24 mm). Then, the length of the bearing will be 774 mm, which will result in the inner length of the extension closest to the length of the hive.
We return to the height of the superstructure. The extension is made of a single board, 165 mm wide. The top pieces are not rebated, and the sides have a 13 mm deep rebate in which the frames are hung. The top frame, as we know, is 158 mm high, and suspended in the frame, it reaches lower by 150 mm, because it lies with the 8 mm thick bar. If we leave 2 mm for the boards to dry, we will get the height of the extension inside 152 mm, and outside, together with the edge of the rebate, 165 mm.
The rebate in the extension should therefore be 13 mm, so that if it is necessary to erect a second extension, any additional devices could be avoided, except for the upward cuts in the beams of the frames (as in Fig. 2 b). When storing superstructures in stacks outside the hive, the high rebate creates a gap at the bottom of the frames and prevents them from piling up, which is harmful*), in case of small inaccuracies or accidental putty or wax residue on the bottom of the frames.
The superstructure frame is 240 mm wide, 158 mm high and has 8 mm thick beams, of which the upper one is 264 mm long, 50 mm wide, side and bottom bars are 36 mm wide. There are no spacer nails. The extension comes with 15 or 14 frames. The width of the upper frame may vary from 48 to 50 mm; such differences will facilitate the tight positioning of the frames when the sides of the upper bars will be a bit bee-damaged. Super boxes should generally be 50 mm wide and should not be narrower than 48 mm if we want the brood to not go to the super box. After setting the frames in the extension, sometimes there is a vacuum that cannot fit the frame, this place is covered with a slat.
*) Due to easy access for mice and dust.
Beehive boarding. The gables are not boarded. Their lower edges reach the bottom and cover the gaps at the bottom joint. The ends of the gable boards protrude, like wings, beyond the sides of the hive 60 mm each, and a rebate 24 mm wide and 10 mm deep is grooved in their ends (Fig. 6 e). Boards 10 mm thick are nailed to these frames along the hive. The shuttering boards are laid in a carp shape, i.e. so that the rebate of the higher one overlaps the planed edge of the lower one (Fig. 7 letter O). The vacuum created between the nest boards and the formwork is filled with dry moss, chaff or shives.
In order for the hive to be better fixed, it is good to put vertical slats in the gap between its walls and the padding (Fig. 6 d). In the rear wall there will be one in the middle, and in the front wall there will be two next to the outlets. They can be inserted with fins (on grating) into the outer walls of the hive box, and the formwork boards are nailed. These slats can be 24 mm thick, 50 mm wide (except for the fin - "trash"), and 570 mm high, i.e. as much as the inside of the hive with the bearing, except for the bottom and the top cover above the gap. Do not hit the nails from the inside of the hive, so that the iron heads do not collect moisture in winter. Before nailing the board, holes are made on the front wall and pieces of slats are attached diagonally downwards, protecting the holes from being covered with litter (Fig. 7 above and below number 9 in the hole).
Instead of boarding, you can only use straw, placed vertically, about 60 mm thick. It is pressed under the horizontal upper 80 mm formwork strip, and fixed in the middle and at the bottom with slats cut from a square-and-a-half. Such upholstered hives, called peasant hives, are much lighter, cheaper and even more suitable for overwintering bees. The outlets are arranged as in a boarded beehive, so above and below the mesh there will be two separate bunches of straw, held in place by two thinner slats, or the line of outlets will get a properly trimmed log, as in Fig. 8.
It is desirable to formwork of the bottom. In boarded hives, this can be done with straw attached with three slats to the longitudinal boards of the padding, which (the padding) together with the tops should protrude 30 mm below the bottom. If the hive is covered with straw, we widen the lower slats by 30 mm as shown in the picture. If the hive is not covered with straw underneath, it is good to put thin straw mats under the nest in winter. Some beekeepers sprinkle - with good effect - peat powder on the bottom of the paper spread under the nest.
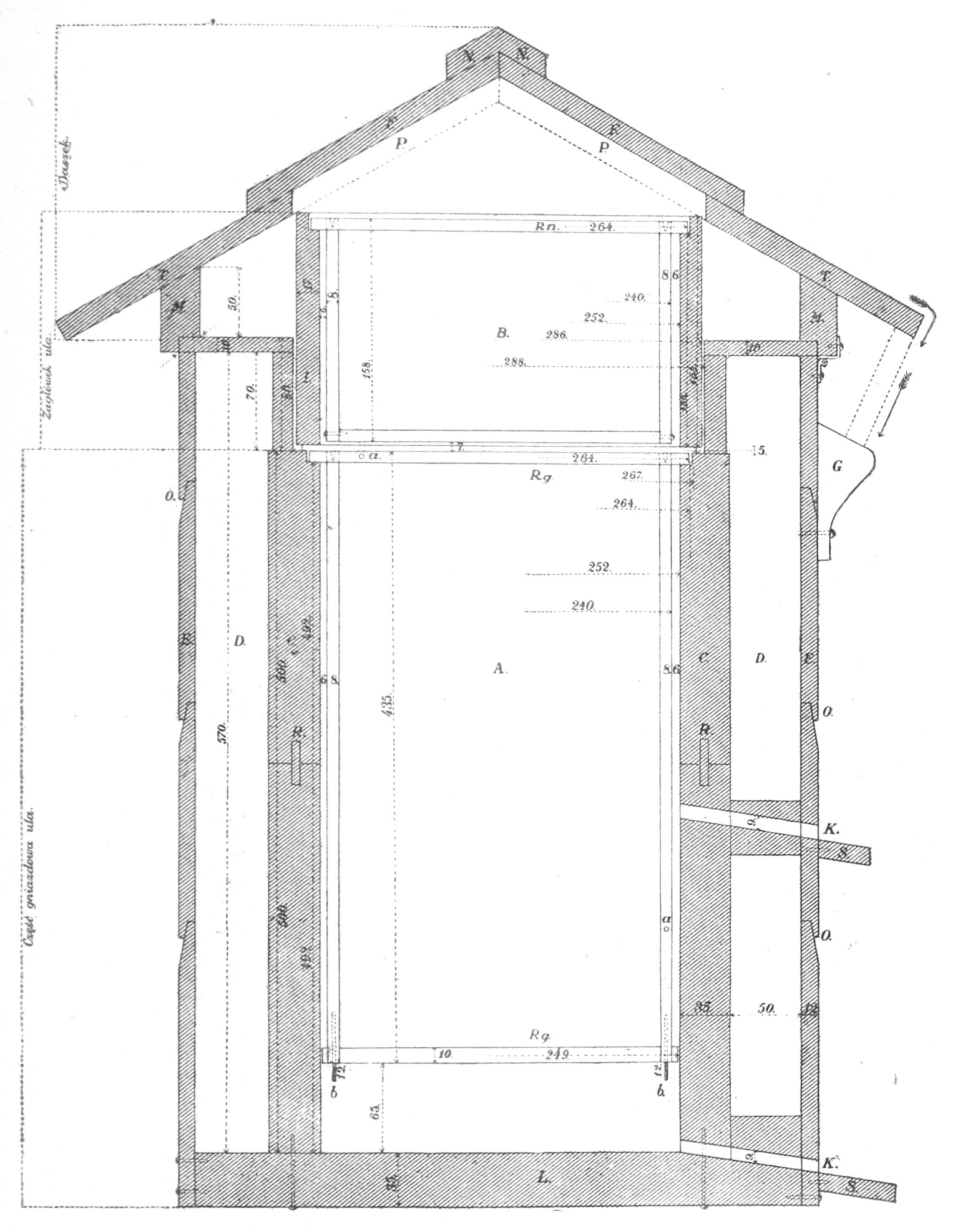
Dig. 7.
Cross-section of the Warsaw hive (own drawing).
A—nest part, B—headboard, C—internal walls, D—a place to put bedding, the whole thing on the left side of the drawing is a form for vertical slats, shown in the previous drawing, letter d No. 6, E-Padding, F-Cop ceiling boards, G-Support, I-Extension, K-Outlets (eyelets), L-Bottom, M-wall panels, N-Strip covering the ceiling, O-Connection of upholstery boards, PT-roof made of boards nailed to the face for covering with ruberoid, etc., R—groove connection (fed, tongue), S—bridges (saddles), Rg—socket frame, Rn—extension frame, a—place of spacer nails, b—bottom nails frames. The numbers indicate dimensions in millimeters. The hinges are located between lit. M G. The arrows between O and M on the left side of the picture indicate the openings of the hive.
We can see from the description that the hive is built without legs and rightly so, because it is then easier to carry and transport, and being sufficiently built, it lasts longer. Moisture-absorbing legs, even if the hive stood on the foundation, rot quite quickly, drawing moisture up to the hull; because they are the entire fixation of the hive, so then the bonds loosen quickly. Anyway, a hive without legs is cheaper, and the pegs driven into the ground under the hives, made of anything, are perfectly suited to their purpose. There is no need to use a good material for the legs.
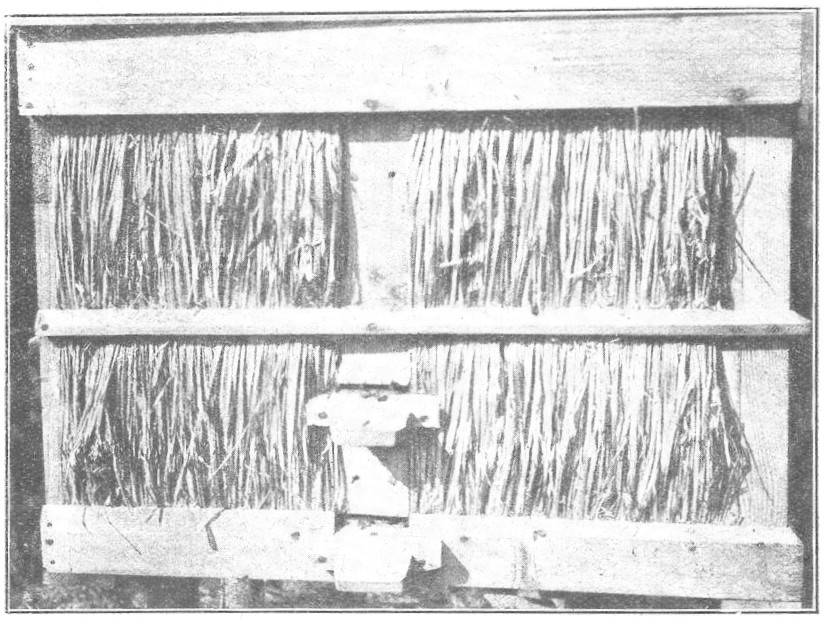
Dig. 8.
Beehive covered with straw without shuttering boards (own photo).
Outlets, latches. There are two outlets in the middle of the front wall: the upper one, located 250 mm from the ceiling, and the lower one, at the bottom, under the first one. Both heights are 9 mm and widths are 120 mm, made obliquely at the bottom, so that little light enters the hive and the wind does not drive rainwater.
Destination of departures. The reader, knowing Lewicki Street, will notice the difference in the dimensions of the outlets. In order for the outlet, used by bees to communicate with the outside world, not to be too tight for a stronger trunk, it must have a sufficient surface and opening. With two outlets 9 mm high and 120 mm wide, the entrance area of 21.6 cm² will be sufficient, and their height will allow bees to pass with ease.
The outlet also serves as a vent for air exchange in the hive. The warm used air comes out through the upper one, and cool and fresh air flows in through the lower one.
The outlet should not allow pests to enter. The most dangerous are: mice in winter, and a death's head in autumn. This August pest can get in through a 5mm gap. With an outlet height of 9 mm, both pests can be easily avoided by placing a fine wire in the middle of the bundle after finishing the bundle.
To protect the trunks from robbing bees and annoying autumn wasps, we put latches on the outlets (Fig. 9). These are plates, perforated with small holes so that the heads of bees do not enter them. These plates enter like dampers into properly bent pieces of sheet metal with a hole cut out for the eyelet. The free movement of the slide makes it possible to adjust the size of the outlet according to the needs and seasons.

Fig. 9.
Outlet latches of frame hives (Italian Fig.).
Apart from the two outlets described, other openings leading directly to the socket are not needed. So we delete the Lewicki outlet at the top of the hive as creating a draft. If we wanted to allocate a hive to a housing estate not only for one swarm, but either for raising queens, or for wintering two swarms unequal in terms of numbers, or for dismemberment - we will treat it as a double (or triple). We can then provide other outlets in convenient places, however, if the hive is used for one swarm, we close the unnecessary outlets tightly.
Some beekeepers are wondering whether a third outlet should not be provided, leading directly to the superstructure. Rather not, because bees bring from the field not honey, but nectar, which undergoes transformations in the lower parts of the combs, and then is transferred to the upper warehouses to the undergrowth. For the beekeeper, this outlet would even be harmful, because the queen lured to it would brood in the super, especially if we had not very deep cells from the artificial hose or poison wax. At the same time, we would encourage bees to deposit pollen into the working combs in the extension, which would unnecessarily burden the extension and significantly reduce the value of honey, giving it an undesirable taste.
Warsaw Street 2
The bridge gives under each outlet. It is a small slat, nailed diagonally downwards, on which bees returning from the field sit down. The bridge is tilted for faster drainage of rainwater. The bridge of the upper outlet is not very large, while the lower one is much larger so that it can catch more bees weakened in flight. Some make lower bridges obliquely reaching almost to the ground, attaching them with wires to a stool or beehive.
It is good when the bridges are made of two pieces, connected with hasp hinges, so that the lower one can cover the outlet in winter, which will protect the hive from sudden gusts of wind, snow and harsh sunlight in March.
The roof is double-eaves. Opening angle in the ceiling 120°. The frame of the roof covers the hull of the hive on all four sides with a rib cut in half in a rule. Half of it lies on the edge of the hull, and the lower part of the frame includes ul. Murłaty, i.e. front and rear inch slats, holding the roof along the sides, are quite low, about 50 mm, cut diagonally at the top to hold the eaves boards. The tops of the canopy, also made of a rule rule (24 mm), reach the very ceiling and are closely matched to the form and width of the boards that make up the cover. In order to allow ventilation in hot weather, it does not hurt to make openings in the ceiling tops with flaps for other seasons. Inside, these holes are covered with a dense mesh to protect against pests.
The covering of the roofs is made of planks of inch gauges, overlapped. The boards must be of the best quality, completely without knots, so that they do not let water through. A knot, even if it looks the strongest, will create a gap in a relatively short time, sufficient for moisture to pass through. The gap created in the ceiling by joining two boards should be covered with a separate strip called a wolf. (Fig. 7N).
When constructing the canopy, care must be taken to ensure that it does not leak. It is much safer to cover the roofs with waterproof material. You can use tar felt, as long as it doesn't smell like carbol, but it is not durable enough, so it needs to be changed often. Tarring roofing felt is risky, because bees can abandon the hive. Ruberoid and linoleum, although more expensive, are much more suitable. Some cover the canopies with zinc sheet, to protect against overheating, you should put quite thick newspapers under the sheet, or put a felt, protected against moths*). Hives covered with sheet metal should not be placed directly under trees; for raindrops falling on a rainy day would not calm the bees, but moderate shade is very desirable.
If we build canopies with the intention of covering them with some waterproof material, we do not nail the boards overlapping, but next to each other to the forehead (Fig. 7 P. T.). In order for the rainwater falling from the roof not to damage the walls of the hive, the eaves should be wider and the boards above the tops longer than the hive itself. It should be noted that above the gable where the door is located, the boards should protrude much further.
The roof, adjusted to the hive, moves on hinges that can be dismantled, giving the possibility of removing the roof for the winter when placing it in the stebnik and erecting it in the summer if it is necessary to add second superstructures. Thus, instead of a fixed pin in the hinge, there may be a bent wire.
The open roof is supported by the edge of the eaves on a support nailed in the middle above the eyelets.
The beehive box is built of walls connected with long-groove joints. The side walls of the box are connected to the gable walls with a fin joint. The ends of the gable boards are connected to the boarding of the sides of the hive using a box rebate joint. The boards of the padding (linings) are connected in a decorative way, with the boards being rebated from the bottom. The gable door of the hive, rebated all around, is fastened with a recessed fin. The superstructure can be nailed to the corner and corner joint or finger-jointed.
The upper beams of the socket and superstructure frames are connected to the side beams with the use of a central single round dovetail. (The upper ends of the side bars are pinned into the upper bars). The lower corner joints of the superstructure frame are corner joints.
The ends of the side boards of the beehive box opposite the gable door are terminated with a half fin facing outside the box. The board is smooth on the inside.
*) Do not put arsenic or solutions of copper or iron sulphate under the metal sheet.
According to the technical carpentry vocabulary. Look. Fr. Kuśmierski, Constructions of wooden products. Vol. I. Ed. Kasa im. Mianowski. 1928.
3. Hive supplies. A Warsaw hive requires at least 18 nest frames and 14-15 top frames. In order to separate the nest from the rest of the empty space in the hive, when it is not yet covered by bees, two gates made of transverse squares are needed, held together with fin strips (floors) lengthwise. Their dimensions are almost the same as the inside of the hive, as long as they enter slightly, namely: height 499 mm (including the bar), and width 250 mm. Penstocks are equipped with whiskers for hanging on frames, similarly to socket frames. The slat, serving as the upper beam, is not thicker than a plank. The valves should be made in such a way that, on the one hand, they allow for easy movement, and on the other hand, they delimit the nest so that the bees do not get lost through the cracks.
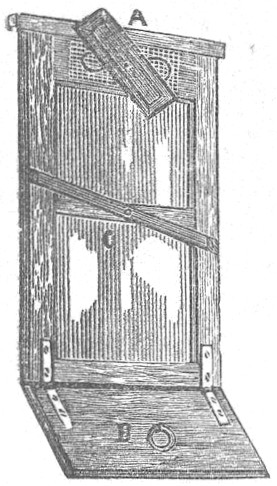
Dig. 10.
Lewicki's glazed valve (T. P. O.).
In addition to the above, it is good to have another valve with a total height of 499 mm, built like a frame, with a flap on the straps at the bottom, 60 mm high, used to sweep the hive without disturbing the bees too much. This frame is filled with glass, which should not be putty, but fastened with small nails. The glass valve (Fig. 10) is used for easier observation of bees during their summer development and replaces the usual wooden one. It can replace another valve in the cold season, but then it must be on
place the glass, insert a suitable piece of slat. Otherwise, moisture accumulating on the glass will negatively affect the condition of the bees.
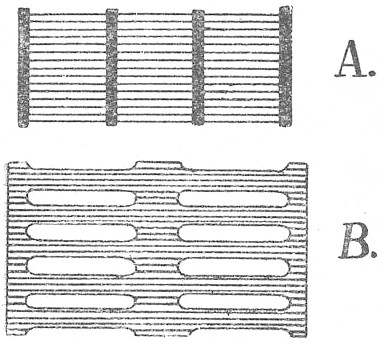
Dig. 11.
A grille, B a piece of partition sheet.
The metal sheet or barrier grating has already fallen out of use in progressive bee-keeping, but before the spread of the artificial hose and the use of extensions, it played a great role during honey harvesting. The grille is made of round wires connected by narrow metal slats. The distance of the wires from 4.2 mm to 4.3 mm allows bees to squeeze through, while queens and drones, being larger, cannot get through the grille (Fig. 11). The bars were a great nuisance, torture for the bees, and the sheet metal was a knife for their wings.
The task of the trellis was to keep the mother away from the honey cell, from where unreddened combs could go unhindered to the honey extractor. The use of trellis, despite the torment of bees, significantly increased the efficiency of apiaries in its time.
The baffle sheet should be absolutely removed, while the wire grille should not go completely out of use, because there are cases, albeit exceptional, when its use becomes necessary; so it's good to have a pair in the apiary. The grille is placed in a broken frame valve.
In conclusion, it should be mentioned once again about the valves that from the side of the combs, all valves should be made as possible without notches or frame depressions, because strong bees do not like the slightest unnecessary vacuum in the hive and pull the cells in places where the valves are uneven, distorting the surface of the combs. Therefore, the beams of massive valves should be equal to their surface, and frame valves should be built in such a way that after inserting glass or plywood into them, they form one even plane. The same applies to the check valve device.
Spacer pins are given to all valves in the appropriate places.
The top-mounted hive has a loose passage between the upper beams of the nest frames to the headrest. Such a nest cannot be directly covered with a board, because the bees would seal the frames and be disturbed when opening them; so we put a cloth on the nest. It can be varnished or not, but it should not be old or mangled, as it would be quickly eaten by bees. The best is sackcloth, quite thick, straight from the art, if possible without wool, so washed. It should be long enough to cover all the nest frames along and across the hive, if necessary, - the headboard from edge to edge. Half the width of an ordinary homemade product is enough for the width of a hive.
On the canvas we put the so-called a pillow. It is a rule board, fastened with fin strips, 286 mm wide, any length, it can be about 450 mm.
The superstructure should have at least one penstock, built similarly to socket valves, so hanging on the whiskers in the frame and tightly reaching the top of the frames, i.e. 163 mm long and 250 mm wide. These valves are sometimes needed when this year's swarm, placed on ready-made frames with built-in wax, bears honey immediately in the first year. We usually plant a new swarm on 9-10 built-in nest frames, so the cover with the extension should not be wider either.
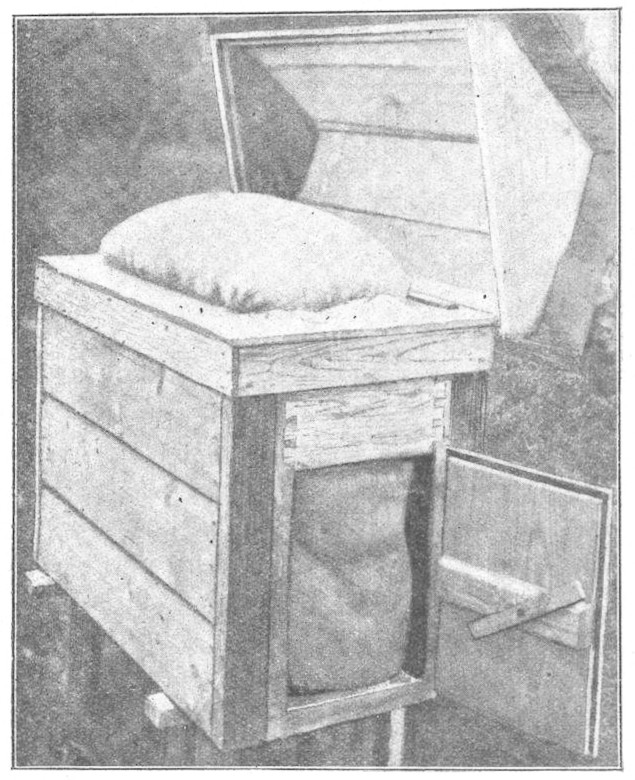
Dig. 12.
A hive equipped with bags filled with chaff for the winter.
Details of the door-valve device (own photo).
A hive boarded on only two sides would be too cold for winter. So, in order to completely protect the bees from frost, we surround the nest with straw mats on both sides and in the headboard, instead of a wooden roof, we put a straw mat. Mats can be replaced by bags filled with dry forest moss, oat husks or chaff (Fig. 12).
Side straw mats have the width of the inside of the hive, and the length is the same as the height of the hive inside to the top of the nest frames, i.e. 500 mm. The mat, which serves as a pillow, is 400 mm long and 286 mm wide.
How to sew mats. To prepare straw mats, you need a workshop, desirable for every beekeeper. It is a stool on whose plate (top) there are two rows of posts placed side by side. The rows are 50 mm apart - this is the future thickness of the mats. The distance between the posts is standardized so that longer and shorter mats can be sewn in the same workshop (Fig. 13). The posts are firmly fitted across the board, which is made of hardwood. Behind the uprights, along the length, there is to be a gap e of about 36 mm wide, in which one more moving upright moves along. A strip d is nailed to the edge, forming this gap.
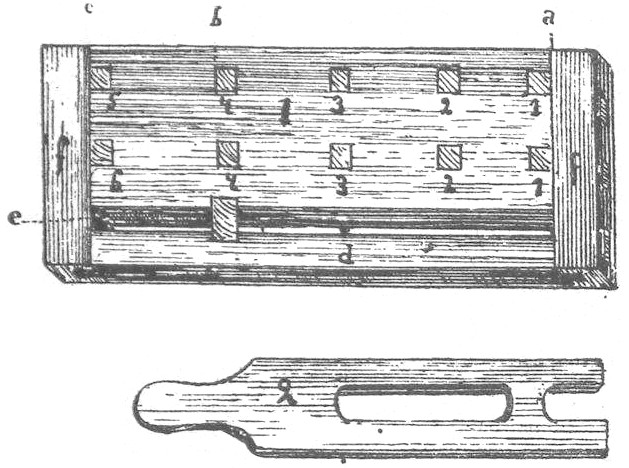
Dig. 13.
Workshop stool plate for sewing straw mats (1) and lever for compressing straw (2).
Four pairs of bars are placed at equal distances from letter a to b over a space of 400 mm—this is the length of the mat-cushion. The fifth post is set so that its edge at c is 500 mm from a to c - this is the length of the side mats.
If during overwintering we intend to place sticks across the nest to enable the bees to pass under the canvas to the neighboring combs in case the honey supply over the nest ends prematurely, the side mats should be made a bit longer, namely: 505-507 mm, so if necessary we can nail the slat to one of the edge posts.
Drill five holes through each pair in the set posts, with the fourth hole at 251 mm from the board, which is the width of the side mat. The fifth needed in only the four posts from a to b, is to be at 286 mm - this is the width of the top cushion mat. In the movable post, we drill transverse holes at the same intervals as in the fixed posts. We give each pair of fixed posts wire hooks at the ends so that they do not come apart when the straw is pressed. We still need a lever to compress the straw between the posts (fig. 13 no. 2).
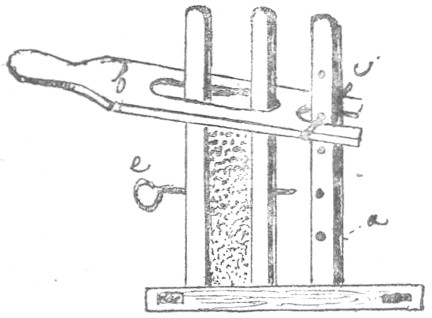
Dig. 14.
Pressing the straw in the workshop, a the lower hole of the movable post, b the lever, c the plug of the movable post, e the plug for the fixed posts, the latter need 5 for a total.
Sewing the mats is done as follows: Between the rows of stationary posts we put handfuls of straw, ears alternately, above both tops of the workshop. We press the straw quite hard with the lever, up to the first holes at the bottom and through them we put the wire plugs that will hold the straw. The wire should be thick enough not to bend under the pressure of the straw, and end with a key-like loop that will make it easy to pull the plugs out. Then we put a new layer of straw, just like the first one, press it with the lever to the second hole and weave it with the wire taken from the first bottom hole, etc. (Fig. 14). When we reach the height we need and we have a wall between the posts, limited on top with plugs (Fig. 15), we proceed to sewing the mat.
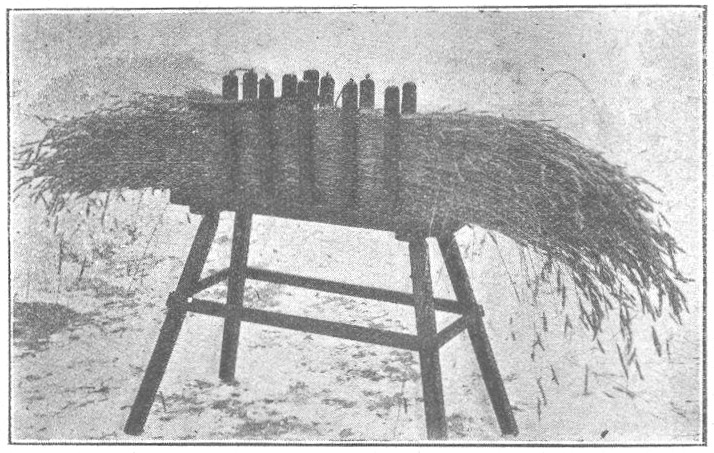
Dig. 15.
Straw pressed in the workshop to the height of the side mat (own photo).
One plug is enough for each pair of stationary posts, five in total, and for a movable one, which is loose in the gap, lit. e (Fig. 13), also need one plug to rest the lever (letter c Fig. 14). The plug of the movable post is placed gradually higher and higher as the work progresses.
By squeezing the straw, we give it medium compactness, so that the mat does not wobble after sewing, as it is too soft, but also that the straw blades are not crushed, because then the mats would not be warm.
Stitching is carried out in the manner indicated in Fig. 16. Sew with galvanized wire no. 18-20 (in the absence of wire, varnished twine), threaded into the eye of a simple needle made of hard wire. The figure sufficiently explains the method of stitching, but it should be noted that the first step is to tightly wrap the mat around with wire; then, running diagonally through, we cover the straw with a twist stitch, attached to the wire around the mat, and return to the opposite side. In the figure, the beginning of the work is where there is a straight arrow at the bottom right. Follow the direction of the entire line, paying attention to the pointing arrows, and the whole process of the work will become perfectly clear. Figure 17 shows the sewn mat ready for use.
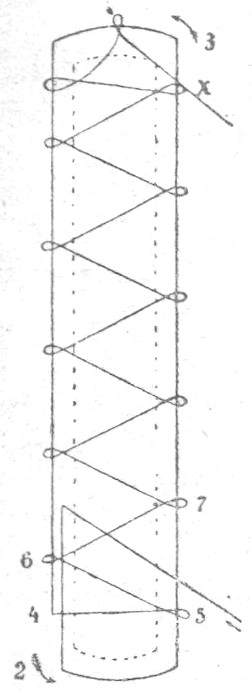
Dig. 16.
A stitch used when sewing straw mats.
When sewing side mats, we put straw only up to the fourth holes and cut it flush with the posts at lit. a and c (Fig. 13). The mat-cushion will reach the fifth holes and will be cut at the b-pillar in the same figure. The protruding ends of the straw are cut with an old scythe along the outer line of the a and b posts for the cushion mat, and along the a and c lines for the side mat.
The feeder is a trough almost as wide as the inside of the hive, oblong, not too high to fit under the frames on the bottom of the hive. It should be tightly packed so that honey does not pass through. It is used to feed bees in poverty when we do not have spare honeycombs. We prevent the bees from drowning by making a raft of clumps, which we put in the honey given to the hive under the frames. In the absence of a raft, sprinkle honey with clean chaff or wax crumbs.
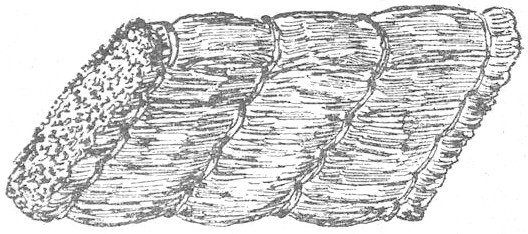
Dig. 17. Sewn mat.
A feeder made of a bottle, clogged with an ordinary cork, in which a glass or metal tube is placed, cut diagonally at the outer end, is very good for feeding the bees. The bottle, poured full and plugged with a cork with a tube, is turned upside down and the end of the tube is placed at the bottom of a narrow trough. The satie flows until the liquid covers the obliquely cut opening of the tube, so there is no fear of overflowing; and from the bottle it will gradually decrease as the bees take their satiety from the trough. The trough can be placed on the bottom of the hive and the bottle can be placed in the corner next to the valve; however, it is better to build a tray that would fit in the socket frame just below the upper bar at a distance of 6 mm from it (Fig. 18). Such a frame with a crossbar can be filled from the bottom with an artificial hose. The built-in frame then fulfills two tasks: comb and feeder.
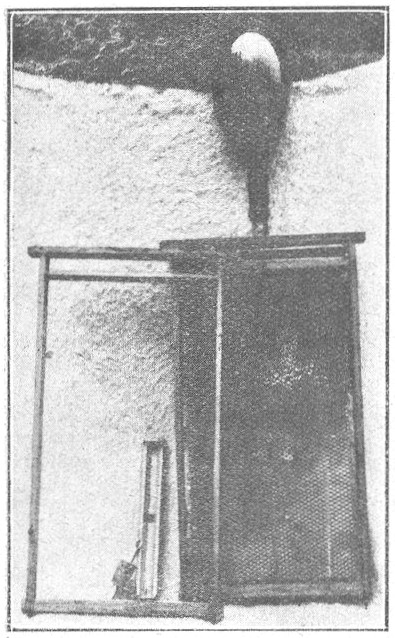
Dig. 18.
Feeder with a cork (own photo)
It is equally well suited for stoking and feeding the Müller feeder, attached lower in the cross-section (Fig. 19). The general perspective view of the feeder is presented in Fig. 24.
The described method of feeding bees has the disadvantage that the cork feeder can only be used to feed bees three times full or thinner, because honey, being too thick, will not flow through the tube.
4. How to transform Lewicki Street into a Warsaw superstructure. Our famous beekeeper introduced two types of hives: the first type has double roofs, the second type has a uniform double-eaves roof. The first one is a very beautiful beehive whose front half, intended for overwintering, is covered with straw and has two outlets at the top, while the rear one without padding, has an outlet only on the side (Fig. 20 and 21).
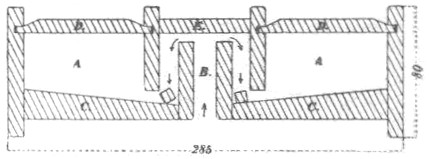
Dig. 19.
Müller's feeder in cross-section (own drawing).
A chambers for honey, B entrance for bees, C slanted bottoms in chambers, D chamber caps as latches.
By remodeling this hive, we make a uniform roof, but its front half can be used by extending it to the entire hive by means of a piece. The pieced roof should be upholstered with a dense material so that it does not leak. The rear part of the hull, not boarded, is covered in a similar way to the front one and we build up the headboard of the hive to a height of 80 mm, using the method described in the construction of the superstructure hive, creating a nest for the superstructure. You can simply, after removing the roof and completely covering the hive, attach additional slats of appropriate thickness on the inner walls of the hive, all the way up, with the width of the nest of the extension being 288 mm. In the tops of the headrest, the crossbars should extend to the outer padding of the side walls. Board the superstructured part on the sides, and then fit the roof. The gable hinges should be removed and moved to the upper edge of the superstructure of the front wall, as in figure 7 between the letters M - G.
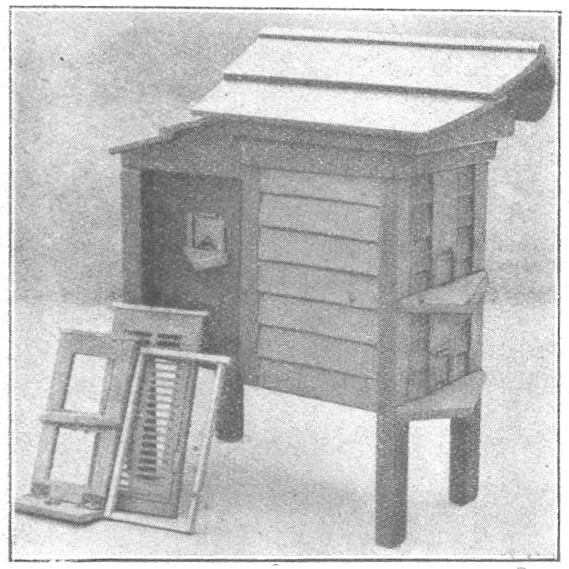
Dig. 20.
Lewicki Street with a double roof, type 1 (own photo).

Dig. 21.
The same street is open (own photo).
Before starting the beating, we delete all the outlets, and in their place we arrange two in the middle of the front wall. If we leave any former outlet for special purposes, remember not to create drafts.
The second type of Lewicki's hive - peasant hive - with a uniform two-eaves roof will only require the addition of walls and improvement of the outlets. In both cases, the upper superstructured part of the hive will take the form indicated in Fig. 7 in the place marked with lines and the inscription "Hive headboard".
The frames in the hives in question have the correct dimensions, the only difference being that their bars, which come together at the top, are 36 mm wide; they should be - after checking if there are no nails driven in anywhere that would cut the plane - they should be planed. The procedure is easy when the frames are empty, but they can be brought to the desired condition and covered with wax, and even with brood and loaded with honey. In this case, to the removed door or simply to the smooth wall right next to the corner of the building, we will nail a horizontal slat of the length and width of the frame beam, protruding 2 cm above the wall level. At the end of this slat, we will drive a fairly strong pin into the wall, protruding 20 mm above the top of the slat, which will be used to support the beam of the frame during planing. Below we give a stand to support the frame that is in the robot. We plan the beams of the frames standing up so as not to place the combs loaded with brood or honey horizontally. Does not matter. if during planing, despite being careful, the upper part of the comb surface is slightly damaged - the bees will quickly repair this damage.
After shaving the beams, we put spacer nails in the right places. To avoid shocks from hammer blows, the places intended for nails should be punctured firmly with an awl.
5. Changes in the Warsaw top hive. The deviations that can be observed in this description from those given by other authors are slight. I only returned to the dimensions of K. Lewicki's (father's) hives and, using the extension, did not accept the changes introduced under the influence of the dadans by the well-known author St. Brzósko. Against normal behavior. dimensions of the frame, the width of the hive and the supers, these deviations will not make any difference to anyone who already has Warsaw super hives.
The positive aspects of the hive described by me are as follows: it combines two systems of hives - the Warsaw top and the ordinary Lewicki. Having the advantages of both systems, it removes the disadvantage of the removable bottom, makes the construction of the hive cheaper, because the material for the legs falls off, and the durability of the construction is increased; through the glass in the valve allows you to observe the bees through the valve in the summer, when it is most desirable - before giving the super; in accordance with the needs of bees, it guarantees good air exchange in the hive; removes moisture from the bottom and finally allows the use of a checker if necessary.
It remains to add one remark, rightly recommended by other authors: one should diligently observe the dimensions in millimeters, have good and accurate rulers. So far we had Polish inches (24 mm), Russian inches (25.5 mm), then Prussian inches (25 mm Reinland), and finally English inches (25.25 mm). Thus, in a hive built according to any of these measures, we will find much different dimensions than in the original Lewicki's hive.
A beekeeper who has several hives so faulty, let him go no farther, but proceed with his work with good measure. And let him repair the hives he has by fitting in additional slats and slats, or get rid of them gradually. It is a great nuisance for a beekeeper when, at work, in the most critical moments, he is disturbed by unequal dimensions of hives in the apiary.
We have so far omitted one less fundamental but important detail. Namely, we did not take into account the prevention of bees pulling robots under the frames. This treatment is needed only in the summer, i.e. at the time of the greatest development of the strength of the trunks.
Well, there are two ways: 1) proper construction of the hive with side pads for the winter nest and 2) device for the summer of triple plywood supports just below the frames.
The first is to build the hive with the frame placed lower so that the frames hanging on it are almost resting on the bottom of the hive with the nails protruding from the lower beams. Bees will not build there for fear of vermin and mold. Although there will be 13 mm of free space under the frames, they will not build it up. On the sides and top, gaps larger than 7 mm would be drawn.
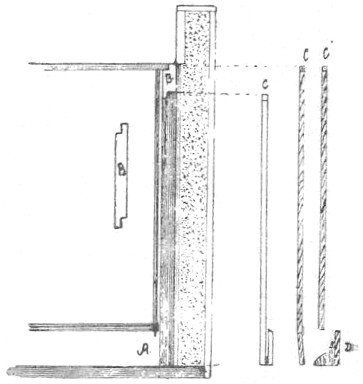
Dig. 22.
Part of a cross-section of a Warsaw hive arranged in the Szreder way (own drawing).
After setting the rebate slat B, a gap will be created under the frames A, needed for the winter for air exchange. C valve with the flap down and the second C valve with the flap up. C and D the second method of valve device.
Such a distance from the bottom, sufficient for the summer, would be harmful as too small for the winter, so when arranging nests for overwintering, we hang the frames higher on properly matched slats, the length of the winter nest; these slats raise the nest to the desired height (Fig. 22 B).
With this solution, the side valves should be shortened to the extent that the frames are lowered for the summer, and for the winter, a further sequence of them in the form of transverse slats should be added under the lower end of the valves, with arms inclined towards the center, which should be turned under the socket so that they do not interfere in close proximity to the nest with straw mats (fig. 22 D). Mats in this case remain unchanged. This is the idea of Mr. Józef Szreder, a passionate beekeeper and former manager of the carpentry workshop at the Beekeeping and Gardening Museum in Warsaw.
The second way to protect yourself from unnecessary construction is a slide under the frames, which can be set on pegs or inserted into the rebate arranged in the side walls of the hive below the frame.
Both of the above methods are good, but they have a disadvantage: they create cramped conditions in the hive and do not allow the bees to hang under the frames (which they like very much). Therefore, in order to prevent lack of space, it is advisable to provide two extensions and arrange the height of the headrest accordingly.
6. Material for hives. It should be dry, unused, but it is not necessary for it to be good. Old, rotten boards, useless for almost anything else, trimmings, remnants, even taken from an old demolished building, floors, ceilings, formwork can be used - but they should not be rotten or infected with fungus.
Not having similar materials at hand, it is best to buy middle boards - core, because they are the least subject to drying and warping. The best tree will be the so-called deficient, with healthy red muck. Such boards cost much less than a truly selected material, but they are valuable for the beekeeper, because they are extremely liked by bees, have considerable strength in construction and are particularly resistant to moisture. In addition, mucky wood is warmer for bees, as it is a poor conductor of heat. If, finally, we had to make hives from fresh material, containing a significant part of the so-called white - a new grain - very susceptible and sensitive to weather changes, when nailing boxes, we always turn the side of the board closer to the core outward.
We recognize the middle side of the board by observing its end: the arcs of the rings are turned outward with their convexity, and their ends inward, i.e. towards the core.
Wood, when rubbed on boards, dries more with its whiteness than with its core, for the freshly grown rings are less tight and more saturated with sap of the tree. As the boards dry out, they shrink in the thinner side, i.e. away from the core. Therefore, we nail the less sensitive surfaces of the boards outside so that they do not stick out with their edges while drying and do not create gaps in the hive. Then, at worst, they will arch a little outwards with their centers.
Speaking of fresh material, I do not intend to advise building hives from wet material.
What I have said about muck applies to the box and (too bad) the lower part of the roof, but these remarks should not be applied to the boards covering the roof of the hive. When the boards are not to be covered with a waterproof material, they should be of the best fit and without knots, as we have already mentioned.
In addition to the wood material described, any other material can be used. The condition is that it should be porous, not compact, so it retains heat. The best material is always straw, hives made of it are cheap, light and warm, and cool in summer, because they do not let the sun's heat through. It is very good to combine wood with straw when building hives.
7. Painting the hives. The hive, completely finished, is simply coated with oil paint.
The hives should be painted in different colors, but the roofs and hulls can be given different colors in different combinations. Shades of blue are the most liked by bees. Darker colors are better.
In order to protect the interior of the hives from the moisture that accumulates inside and does not dry out through the pores of the tree painted on the outside, some advise also to paint the hives once and inside with oil paint. For painting the interior, it is best to use varnish made of beeswax and beeswax. The varnish is prepared as follows: the bee putty is washed in well warm water with the addition of sulfuric acid. Dry, cleaned putty dissolves in warm linseed oil in the following weight ratio: putty 1, wax 1, varnish 4. To make the appropriate varnish for this varnish, place the linseed oil in a warm oven and steam it there for 14 to 20 days without cooking. The varnish, made on such varnish, is resistant even to boiling water - so that in some countries they even coat wooden kitchen utensils with it. For painting hives inside, the varnish can be prepared less carefully.
8. Cheap Warsaw high street. We have described the construction of a beehive made of boards, which is quite difficult and expensive for a self-taught person. Currently, I am giving you a way to tinker a hive at home with almost no tools, it is light and cheap, built in the Dzierzon way.
A box with internal dimensions of a Warsaw hive: 252 X 750 X 500 mm is made of thin slats from goods boxes. The boards are to be nailed crosswise. The outer corners of the box do not protrude, but are compacted into straight corners. The bottom, nailed across from the same slats, protrudes 50 mm in all directions. Frames can be hung on the upper edge of the box, so the edge will serve instead of a frame made in a half-track in the previously described construction (Fig. 23). At the top, we wrap the box around with slats made of the same slat, the edge of which will protrude above the top of the box by 80 mm, and have a width of about 110 mm. On top of the mentioned slats, we nail a frame made of rulers, having the same light that was created in the middle of the box after nailing the slats. In this way, a rebate for hanging socket frames and a headrest, i.e. a socket for an 80 mm high extension, were created.
Departures are made in the right place.
We cover this hive with a straw braid around it in two rows, and so that the openings are not clogged during the beating, we nail bottomless boxes made of thin slats 50 mm high and a useful hole 9 mm high and 120 mm wide opposite them.
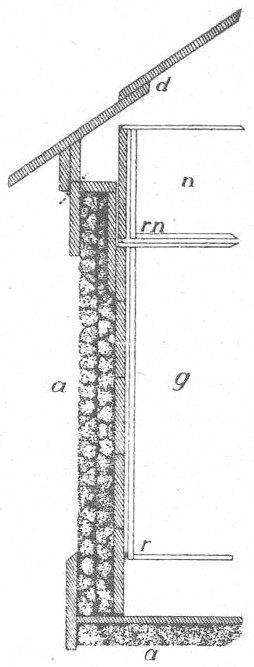
Dig. 23.
Cheap Warsaw high street (own drawing).
a side - braid encircling the hive double, and bottom - bottom padding, d part of the roof, g nest part of the hive, n header, r bottom of the nest frame, rn top frame. The arrows on the top left indicate where the hive opens.
In one of the gables, we cut a door, which is supposed to be slightly narrower than the door of an ordinary hive, because reaching to the very walls, they would make a breach unbound, so to prevent this, in the middle of the hive, in the corners of the gable, where the door is to be cut, we nail triangular slats. At the same time, they will fill the corners created by the side spacing, where garbage would accumulate during sweeping. So we make a door 220 mm wide (or narrower) and cut it out; and so that they do not fall apart during carving and further work, we join the slats that are part of the door with thin slats, as if with pins. For the time being, we attach the cut-out door from the inside with slats so that they do not fall out while wrapping the braid.
Warsaw street. 3
Then we weave braids of straw, similar to the ones for doormats, and we guide them horizontally, starting from the top, closely, once in a while, down the whole box, with the edge of the braid to the wall of the hive. Similarly, we beat the bottom, concentrically starting from the center. If we failed to weave braids 50 mm wide, it won't hurt, and it will even be better if we guide the narrower braids twice, hitting the recesses between the braids of the first row the second time. This will create a quite beautiful-looking wall, compact enough to protect the hive from frost and overheating of the sun.
The described skinning will be sufficiently durable, and having support on the ends of the bottom slats, it will not slip off; and in order to prevent any further damage in the case of some small defect or breakage of the braids, as is the case with hand-made laces, we can nail them from the inside of the hive with wooden nails, and intertwine the braids with sticks from the outside.
After finishing bedding with straw, to the edge made of ruler and nailed in front on the headboard of the hive, we attach quite wide slats around, with which we gird the hive again. We do the same at the bottom, nailing the slats with half to the protruding bottom boards (Fig. 23 a - a). The slats falling down cover the side of the braid that protects the bottom.
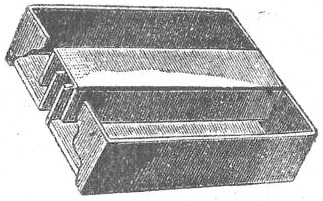
Dig. 24.
Müller's feeder also serves as a pillow covering the nest. Cross-section of the feeder see page 26.
We proceed to the device of the door. Through the gap, created by a ball when cutting the middle slat for the door, we cut the straw through with a crooked beekeeper's knife; everyone will understand that such a job would cause this part of the covering to fall apart. first, we nail double frames to the straw, smaller ones, made of slats corresponding to the size of the door, and larger ones, corresponding to the doorposts - and we connect these frames tightly: one with the door, and the other with the wall of the hive.
Warsaw straw beehive.
9. Overview. Frame hives can be built entirely of straw, but only if the nesting part and the headboard are built separately. In the Warsaw hive, where these two parts are connected, it is impossible to do without a board, at least in the headboard part, where it is about the exact suspension of the nest frames and the placement of the superstructure. In our hive, the headboard will be made of a board from the inside, and the rest of the interior and the entire outside of the hive will be made of straw. I will not justify why we should build from straw, the readers themselves asked for it, so all the reasons are known to them: however, when starting to describe a straw hive, I should point out that building it is not easy. : determining the simplest and at the same time accurate ways to solve this problem. So it is an original but not easy idea, which is impossible to implement without first thinking through the whole description.
Looking through the recipes given by other authors for various hive systems, I had three ways to make a hive: 1) a hive composed of walls - straw mats, sewn on a simple workshop, 2) a straw hive made of three walls and the fourth top wooden, which should be work on a square rule and finally 3) st described here. We will build the entire hull of the hive at once on the finished board, but it will be built from the top, i.e. from the headrest, i.e. turned upside down. I wanted the straw hive to be a real straw hive, which is also mentioned in the title of the brochure.
In order to answer this task, we need to change some less important details in the straw beehive, given in the description of the wooden beehive:
1) there will be no roof in the current concept, but it will be a separate structure, made of either straw mats or narrow patches and covered with straw:
2) instead of the roof, we will give a cover made of straw as a mat, which will cover the entire body of the hive and will be sewn like a door. In order to protect against certain difficulties, we will leave a 50 mm high foil under the cover mat, so the headrest of our hive will measure not 80 mm, but the entire height of the extension and the foil added to it, i.e. 215 mm (165+50 mm. (Fig. 26 P J).
In all other details, the hive described here is to be built strictly according to the description as above for a wooden hive. Therefore, if you want to start building a rule for a straw hive, you must carefully study the entire brochure from the beginning.
On page 23 and following of this brochure, I described a workshop for making straw mats. This workshop will be needed for the straw hive for sewing straw mats useful in ours, but it is also to be a school workshop. The one who starts building straw hives will first prepare this workshop and sew several mats strictly according to the recipe; he will learn in advance to overcome the difficulties of sewing and get used to working with straw. It is a simpler job, and he will approach the more difficult one with some preparation. You need to know the mistakes that can happen and their severity, feel the right tasks of all activities, familiarize yourself with the workshop and master the technique. A straw mat can only be compared to a board, and a hive to a complex building.
A workshop for sewing mats is easy to make at home, it is a small and cheap piece of equipment, while a regular one is much more expensive, both for its complicated construction and for the more select, hard and worn material from which it is to be built. as well as for the care in workmanship and strict adherence to dimensions. This work, therefore, should be entrusted to a skilled carpenter, who will be willing to follow strictly the instructions of the beekeeper, and the latter will study as carefully as possible all the details of the drawings and the description of the rule, in order to avoid unforeseen doubts during construction.
The thickness of the walls of our hive, unlike the thickness of an ordinary straw mat, is 95 mm.
10) Rule. Figure 25 shows a table top width of 762 mm. 1260 mm long, to which 32 posts fit, spaced apart at appropriate intervals and places indicated in the drawing. Four horizontal rows of bars will form. and between them a street around, marked with the letters A, B, E, F. In these streets we will lay and stuff straw, bending it in the corners. The walls of the hive will form from this.
To build the tabletop, we will use old hardwood rulers, they can be oak, maple, ash or acacia. We will build a plank in the shape of a plywood, glued flat from four inches laid crosswise. and then tightened with strong screws in the amount of 20 pcs.; the screws are screwed in half an hour after gluing, before removing the planks from the carpenter's screws (screwdrivers), in the places marked in the drawing. For the heads of Screws, you need to prepare small recesses on the top board before gluing, so that they do not protrude above the surface of the planks, and for screws, drill holes with a slightly smaller cross-section after gluing. to allow screwing in and avoid breaking them.
Do not use thick uniform logs for the worktop, because a compact tree has its own laws: it shrinks and twists under the influence of changes in moisture and heat. The best-laid sheet, seemingly dead, will slightly deviate its surface during atmospheric changes. but at 95 cm the changes will be so great that there is no question of exact construction of the hives.
After removing the pincers, the sides are carefully cut, both surfaces are planed, and then the places for 32 posts are marked out, making sure that the rows are parallel, and the posts in both the horizontal and vertical directions are strictly rectangular. Care should not be spared on the preparatory work, because the sheet, intended for the base of the rule, is its most important part.
We dig out 32 holes in the sheet pile for posts with dimensions of 50X50 mm across. We will put so many posts in the holes motionless and firmly. Normal posts, of which there are 24, made from a 2 inch (50 mm) oak log, will measure 30x60 mm in cross section. The four outer corner posts (No. 1, 8, 25, 32) are made of thicker material, they will measure 60X60 mm in cross-section. while internal corner posts (No. 10, 15, 18 and 23) due to lack of space must be without heels with dimensions of 50X50 mm. The length of the cut posts is 950 mm. The ends of the normal and external corner posts, 100 mm long, are to be inserted into the panel as tenons, resting their heels on its surface, with the heels measuring 10 mm thick. Thus, the normal posts will be cut for the tenon on one side only, and the corner ones on two sides, while the inner corner posts will not be trimmed, but also have tenons equal to 100 mm. In Figure 25, the heels of the posts are dashed, while the outer corners (1, 8, 25, 32) have lines on both sides, i.e. 2 heels each, the inner corner posts (10, 15, 18 and 23) have no heels and dashes, and all others, called normal, have one side, and all the heels are facing outwards in the outer rows and inwards in the inner rows.
There will be one more central elongated hole in the sheet pile, in the form of a cross at its ends (letter R), 50 mm wide, measuring 750 mm along the length and 252 mm at the intersections. A movable post (number 50) will move freely in this opening, 17 mm longer than the others, measuring 50 X 50 mm in cross-section. The spigot of this post, in contrast to the spigots of the stationary posts, will measure in total not 100 but 134 mm, and the rounding will protrude 17 mm above the surface of the plank. We prepare this section of the tenon for the placement of the upper disc. The lower end of the rounded tenon will also protrude 17 m underneath the sheet pile; on this section that sells, we will cut and slightly wedge the lower sheave. The cross-section of the journal rounded on the lathe measures a scant 50 mm. On this rounded tenon, we will insert 2 discs, each 17 mm thick, with the upper one, resting on the corners of the end of the pillar rounding, measuring 83 mm in cross-section, and the lower one 104 mm. The upper disc is attached to the post in front of it, and the lower one, with a cross-section of 104 mm, after inserting the post into the oblong cross hole. Both discs have round holes 50 mm in cross-section and through these holes they enter the rounded pin of the mobile post. Fig. 25 and 26 letters: T. U.
The fixed posts are inserted into the holes tightly with glue and their lower ends are wedged. In this operation, the greatest attention should be paid to the accuracy of the work: the posts should be placed vertically without the slightest wobble, so that all the distances between them at the top must be strictly equal to the distances marked on the plate. All pairs of posts can be equipped with hooks on top, similarly to the mat workshop described above. Internal corner posts may have two hooks for hooking to two adjacent posts, located opposite them from the outside of the alley, which is even more important because they are weaker, as they do not have heels. For example: o bar no. 10 will hook the hooks of posts no. 9 and 2.
Before inserting the posts, 13 holes with a loose cross-section of 5 mm are drilled in them at appropriate intervals, counting from the heel to the top. The spacing is not the same: you have to hit it so that the fourth pair of holes from the bottom in the side pillars is at a height of 252 mm, the seventh pair at a height of 442 mm, and the last, i.e. the thirteenth pair in all the pillars around at a height of 810 mm. The first height is equivalent to the width of the floor mat and the valve, the second height is the width of the lid mat, and the third is the dimension of the entire hive outside from top to bottom, including the extension socket, foil and bottom thickness.
The top posts (9 and 10; 17 and 18; 15 and 16: 23 and 24) will have fourteen holes. the fifth and seventh holes will be at the same level as before, and the sixth will be between them at a height of 345 mm from the top. This will be the height of one of the tops of the hive where the door-valve is to be placed. (Fig. 26 and 27).
Since when compressing the straw, it is necessary to use plugs on the corners in both directions, the inner corner posts 10, 15, 18, 23 must be provided with holes in two transverse directions, top and side. (Fig. 25 letter W). All corner posts, apart from the described transverse holes, should also have diagonal holes for pins that would handle the bends of straw through the corners of the hive. The plugs for oblique directions will be longer than normal by 30 mm, and the holes will be at the same height as for the transverse plugs in Fig. 26. They will not damage the outer corner posts, but could weaken the inner posts (10, 15, 18 and 23), so you do not need to drill through them, but make recesses 10 to 15 mm deep.
After assembling the workshop, it will be necessary to cut the straw close to some of the posts, so in order to protect them from injury, we will cover the exposed sides with zinc sheet beforehand. It will be on the following ten bars:
No. No. No. No.
1
9
I two pairs C 17 IV pair 20 VII pair 23 VIII pair 24
25 28 31 32
Z. valve 370 mm
—————+
D. bottom 845 mm
—— >
O. covers 940 mm
The dotted vertical rulers indicate the sides of the bars. which we will cover with sheet metal. the arrows at the ends of the lines mean: 1 the height of the door, 2 the length of the bottom and 3 the length of the cover. In drawing 25, the arrangement of the sheets is shown by the letters C. Z. D. O. next to the relevant posts, the letters are placed once on this side, once on that side of the posts, depending on the need.
We will use 1 mm thick zinc sheet. cut into strips corresponding to the thickness (60 mm) and height (850 mm) of the posts, we will insert it with its thickness into the tree (in order to maintain the accuracy of the dimensions) and fasten it to the posts with small screws, the heads of which must be hidden in the sheet.
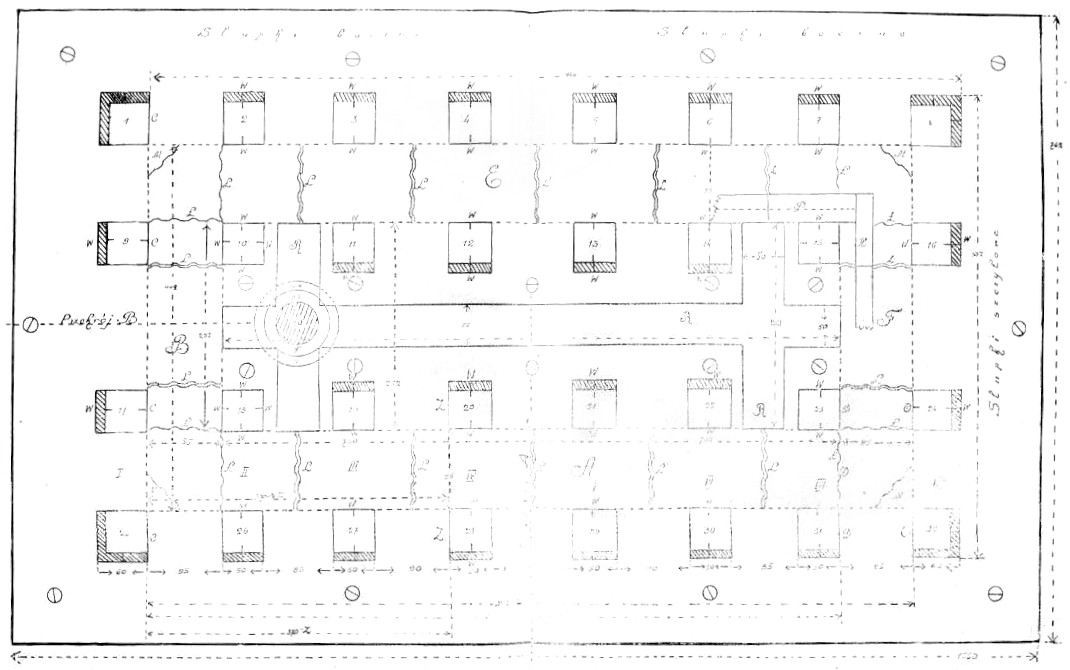
Dig. 25. Workshop plate for sewing whole straw hives.
A B E F - alley for pressing straw against the walls of the hive. Section A shown in Fig. 26. Section B shown in Fig. 27. C - sides of posts to be covered with zinc sheet. D - bottom length 845 mm, right sides of posts 23 and 31 to be covered with zinc sheet. H - headboard top board. L - compound guiding sutures. Ł - straight guiding seams. M - seams cornerstones. O - cover length 940 mm, P - headrest side board; the letters P H show the connection of the side and top boards of the headboard, R - the opening of the cross form for moving the movable post. W - regular plugs. Z - valve mat height 370 mm,
The Roman numerals I to VIII give names to the respective pairs of bars. Broken lines with numbers in them, ending with arrows indicate the dimensions in mm, the same lines without numbers show the outline of the future hive wall.
Numbers: 50 - cross-section of the moving post: 83 - cross-section of the upper pulley T; 104 - Cross section of the lower U sheave in mm.
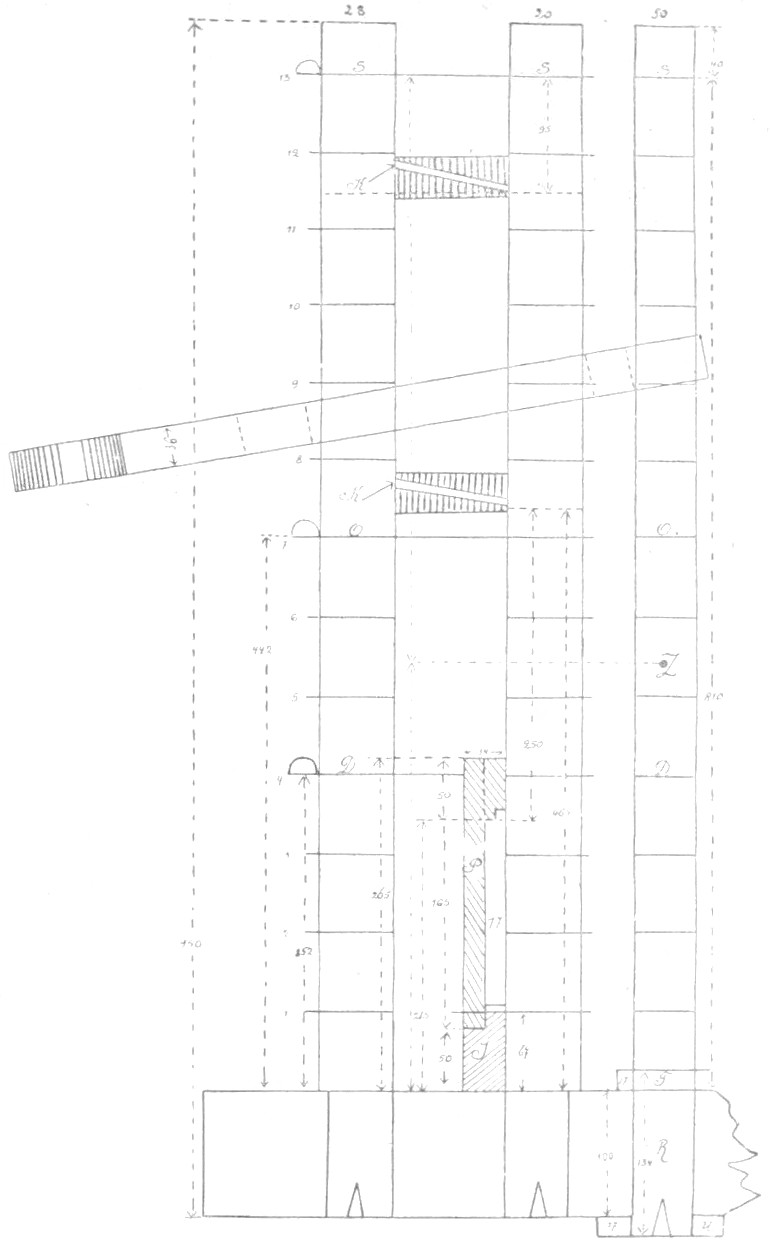
Dig. 26. Section A from the previous figure.
Side section of the workshop rule. D - The height of the fourth plug 232 mm is the width of the bottom. J - cross-section of the board bar. K K - Departures. O - height of the seventh plug 442 mm, is the width of the cover. P - Section of the side board of the headrest. J P - how to set the headrest on the board before starting the construction of the hive hull. R - movable post. S - height of the thirteenth plug 810 mm. T - top pulley move. post. U - lower pulley moves. post. Z - Hole hole on the red side of the post movement. Broken lines and numbers in them indicate dimensions in mm. Numbers: 36—section of the lever shown in Fig. 28. Numbers 20, 28 are the fourth pair of side columns from the previous figure. 50—moving post. Numbers 1 to 213 on the left side of the figure count the stopper holes of the side posts.
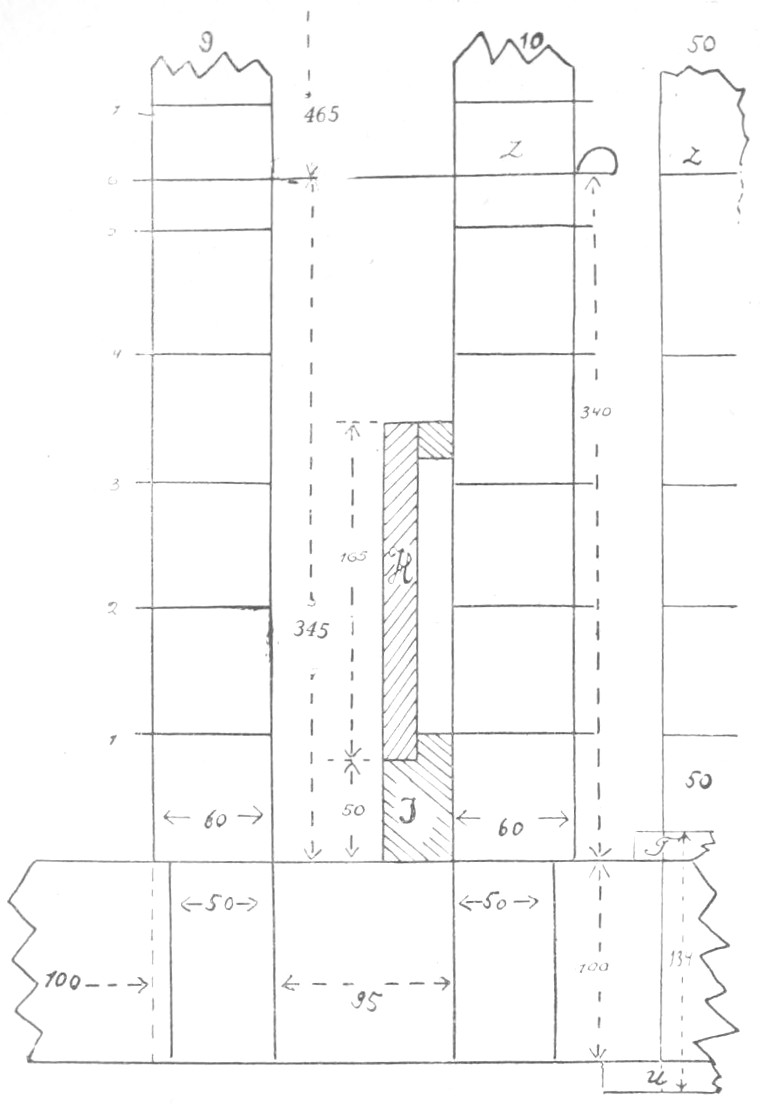
Dig. 27. Section B from Figure 25.
H - cross-section of the headrest gable board. Next to it, at the top, there is a cross-section of the additional device of the board. ] -- cross-section of the rule bar. Z - height of the sixth plug for the valve opening at the top of the hive.
The numbers 1 to 7 on the left side of the drawing count the stopper holes of the gable posts. The posts are broken in the figure, because there was no need to repeat what is in the previous figure. There will be not thirteen, but 14 holes on the top columns, because there are N 6 lit. FROM.
The numbers 9 and 10 are the top bars in Fig. 25. Number 50 - movable post. T U - upper and lower pulley movement of the post,
The rebating of some posts and the insertion of sheet metal into them will be discussed on page 52.
The lever for pressing the straw is shown in fig. 28. We make it from a half-board (36 mm) of oak, 100 mm wide. length 570 mm. The end hole for hooking to the plug of the movable post may measure 52 X 60 mm. At a distance of 29 mm from it, a longer central hole 230 mm long will begin, and then its continuation narrowed - 40 mm. The tapered end of the hole is used to prevent the lever from catching on the bends of the plugs. The long center hole can be partitioned in the middle with a 30 mm slat divider nailed across the top and selected slightly from below above the hole. (Fig. 28A).
From the hard wire 5 mm thick, we prepare 16 plugs, normal long including the loop 250 mm, 8 corner plugs 280 mm long and one for the movable post, which can be half as long.
In the movable post, we make two sets of holes on both sides of its cross-section, one will be spaced as in Figure 20 and the other as in Figure 27. The front and back sides of the post in Figure 26 are painted white, and the two side sides of Figure 27 are painted white red. When making holes on the white side, pay attention to the height of the fourth hole counting from the surface of the plate, i.e. from the bottom edge of the upper disk, letter D (252 mm), the height of the 7th hole, letter O (442 mm) and finally, the height of the 13th hole, letter S (810 mm). . When punching holes on the red side, be careful of the exact height of the 6 letter Z holes (345 mm). Holes on both the white and red side of the post are marked with the letters mentioned above. The white side of the movable post with its marked holes is to serve pairs of fixed side posts, and the red side to the top posts. The relevant holes on the fixed posts are placed at the indicated heights and also marked with these letters. Marking is to prevent mistakes when sewing mats - components of the hive supported by the white side of the post. and leaving an opening in the top of the hive body for the valve. which is supported by the red side of the post (Fig. 26 and 27).
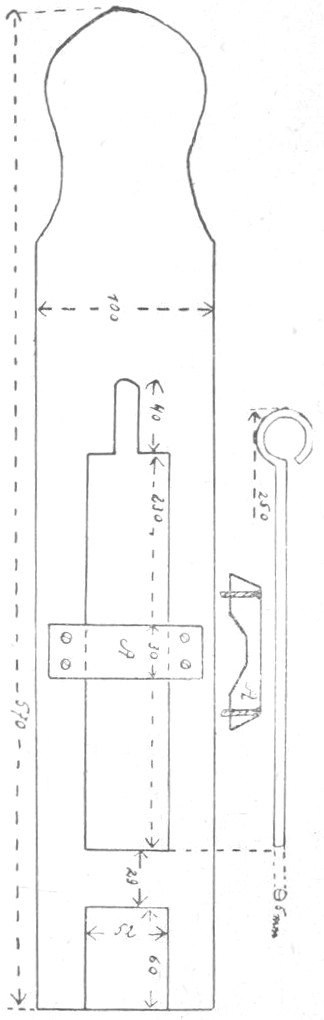
Dig. 28. Lever.
A - slat partitioning the middle hole. Next to it is a 5 mm thick plug.
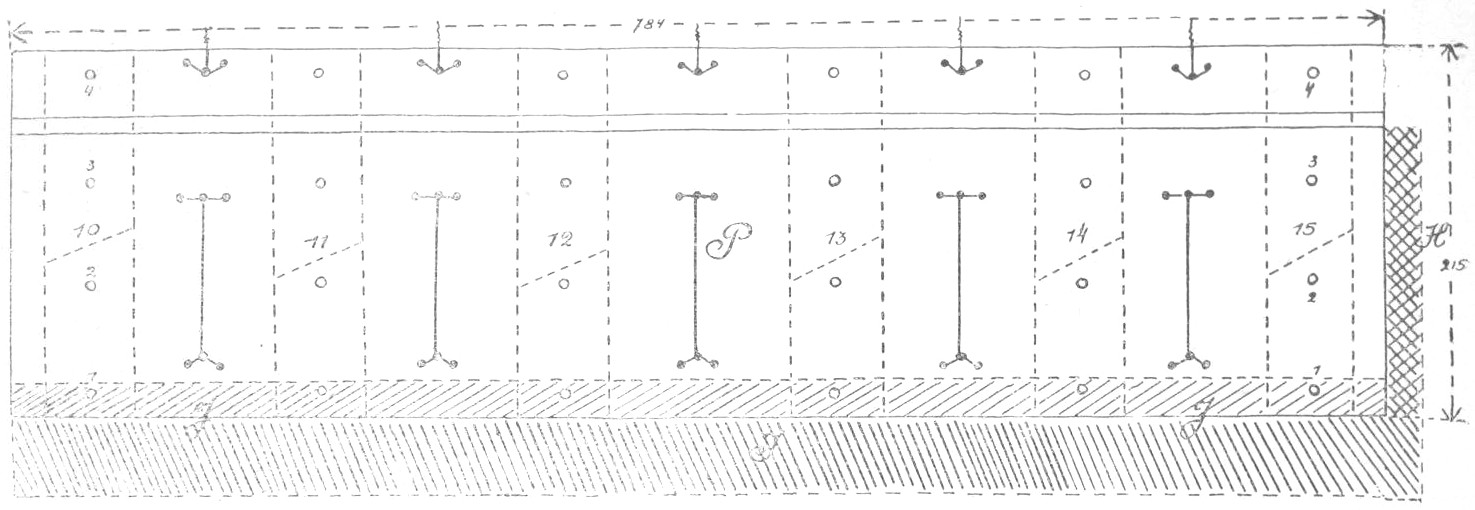
Dig. 29. Front headrest side board.
P - the name of this board in Fig. 25 and 26. J - rule. H - top board of the headrest.
The numbers 1 2 3 4 count the stopper holes of the posts 10 11 12 13 14 and 15 from Fig. 25. The posts are marked with dashed lines on the board. The black lines connecting the dots show the fluting locations and paths for compound (vertical) and twist (horizontal and diagonal) stitches. The dots at the ends of the lines are holes for the wires.
For the entire workshop-rule, we cut the gaps between the posts and corners with grooves in the places indicated in Fig. 25 lit. L, Ł, M, in order to pass the wire for the guiding stitches and under the table top, we will add four strong, slightly parted legs, 200 mm high.
11. Preliminary preparations. Before we start sewing the entire fuselage, we will sew a mat for the bottom, which is to measure 252 mm in width and 845 in length, so we place the straw in alley A (Figure 25) in this way. so that one end of the mat can be cut to the right of posts 17 and 25 lit. € and another to the right of bars 23 and 31 lit. D. The last plugs will go into the holes marked with the letter D in Fig. 26 and on the white side of the movable post, then we sew the mat in a known way.
After removing the sewn floor mat, we will sew a cover-mat in the same side street, which we arrange similarly to the previous one, but we will finish it at a height of 442 mm. by threading the plug at the letter O for the last time (white side of the post), cut it after sewing it on the right side of posts 17 and 25 and on the left side of posts 24 and 32 letter O.
Finally, when sewing the mat for the valve, we put the straw up to the height of 252 mm, and after stitching, we cut it to the right of the posts 17 and 25 and to the left of the posts 20 and 28 lit. FROM.*)
12. Headrest. Before starting the construction of the hive hull, we will prepare two pairs of boards that will be used to cover the headboard from the inside. Figure 29 shows the entire side board reduced. In both boards. measuring 784 mm long, 215 mm high, we drill 5 vertical rows of holes. Each row will have 3 sets of three holes connected along and crosswise with shallow grooves to hide the wires that will sew the board to the straw wall of the hive when sewing.
*) Since the dimensions on both sides of the board are the same,
valve mats can be sewn two at a time. You only need to compress the straw
along the entire street A. The second mat-valve will be cut on the right side of posts 21 and 29, on the left side of posts 24 and 32. In order to speed up the work in advance, it is necessary to provide an additional pair of posts 21 and 29 with zinc sheet after their right side.
The height of the board consists of the height of the extension 165 mm and the height of the rebate with its foundation 50 mm - 215 mm in total. The rebate is to be used to hang the nest frames in the sewn hive, and the foundation, located under it in the form of a piece of a thicker board, will be used to secure the headrest, on the edge of which the entire weight of the nest frames will be hung. The length of the board 754 mm consists of the length of the hive inside 750 mm and the depth of the straw rebate. on which the top of the extension will rest (in both tops of the headrest) 17 plus 17 together 34 mm). The thickness of the boards opposite the headboard measures 17 mm. the foundation, corresponding to the nest part of the hive, measures 34 mm.
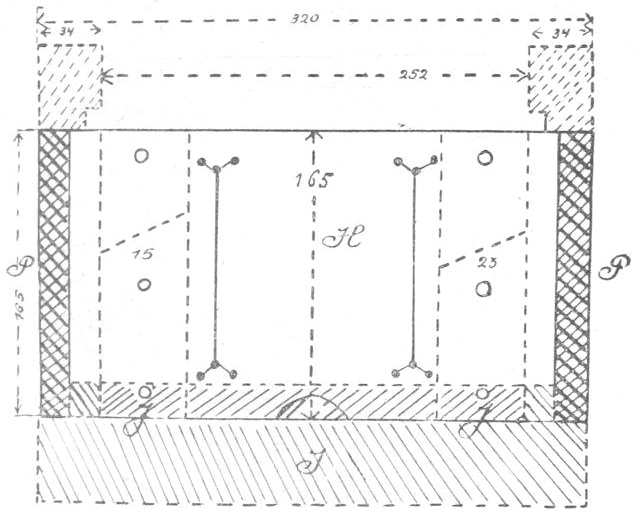
Dig. 30. Front headboard gable board.
H - name of this board from Fig. 25 and 27. J - rule. P - Headboard side boards will be nailed here. Other characters have the same meaning as in the previous figure.
The second pair of even boards (without cross-section) are the top boards of the headrest (Fig. 30), whose height is equal to the height of the extension 165 mm, and the length is 320 mm. which includes the following dimensions: the width of the hive 252 and twice the thickness of the side board, 34 mm each, which is 320 mm in total. The top boards have two vertical rows of holes, and each row has 2 sets of 3 holes. The top boards of the headrest are lowered in the middle with appropriate cutouts for easier removal of the top. The thickness of the gable boards is 17 mm.
To the ends of the side boards: turned with the non-rebated side down, we will nail the gable boards (figure 25 PH) on an even surface. surface. After turning over, we have a rectangular box with a smooth edge around it. It will stand only on two sides (on the foundations), because the tops are 50 mm shorter. Such a box must be made for each hive.
15. Rule. Our workshop can already fulfill some tasks, it can sew mats of various dimensions both in length and in width, but in order to sew whole straw hives on it, it is necessary to build a rectangular rebate frame, which we will call a rule, at little cost and effort. The purpose of the rule is to help in determining the place of the headrest just described for the time of building the entire hive, as well as to leave a 50 mm spacer over the extension, needed in a straw hive. The outer rebate of the frame will be formed by joining two slats of unequal cross-section.
The lower slat measures 50 X 34 mm in cross-section, and the second upper 17 X 17 mm. We will nail the latter on the bottom flush with the inside edge of the frame. The cross-section of the board is shown in Fig. 26 letter J. The frame measures 252 X 750 mm from the inside, it is placed in the A B E F alley and is used to build all hives. The upper slat of the board will separate the sides of the wooden headrest from the internal posts of the workshop, and the lower edge of the same will keep the headrest at a height of 50 mm above the workshop board. The height of the shoe from the inside of the frame is 67 mm, and from the outside it is 50 mm, and the width of the frame is 34 mm. In the lower edge of the frame, from the inside, we make semicircles 17 mm high opposite all six ends of the hole R. This is to make the use of the movable post with a lever available for all pairs of fixed posts. The gaps created in this way where the edge of the disk T entered. See dig. 25.
So we have completed the construction of the workshop and made the components of the hive, now we are about to start building the entire hull,
14. Construction of the hive. In the alleys of the workshop, first place the rule with the frame up. On the board, we set the headrest upside down (the hive is to be built "upside down"), so that neither its top nor the boards will rest on the slab or rest against the posts inside the workshop, but it will rest with its foundation on posts 10 to 15 and 18 to 23 (Fig. 25). The gable boards of the headrest rest only against the frame of the board, they rest on it and do not touch the workshop at all.
However, the gable boards of the headboard are not yet completely decorated, you need to prepare two slats 320 mm long. 17 X 17 mm and nail them lightly to the headboard gable boards at their ends not resting against the workshop posts. We nail them lightly because they are needed temporarily for the time of pressing the straw and will be subtracted after removing the sewn hive from the workshop, after which they will be used in the same capacity when building other hives. The purpose of the slats is to prevent the straw from shedding when pressing down on the walls of the hive in streets B and F and to emphasize the exact rebate in the straw wall. While sewing the walls of the hive, we will avoid these slats. not to be sewn on as detachable.
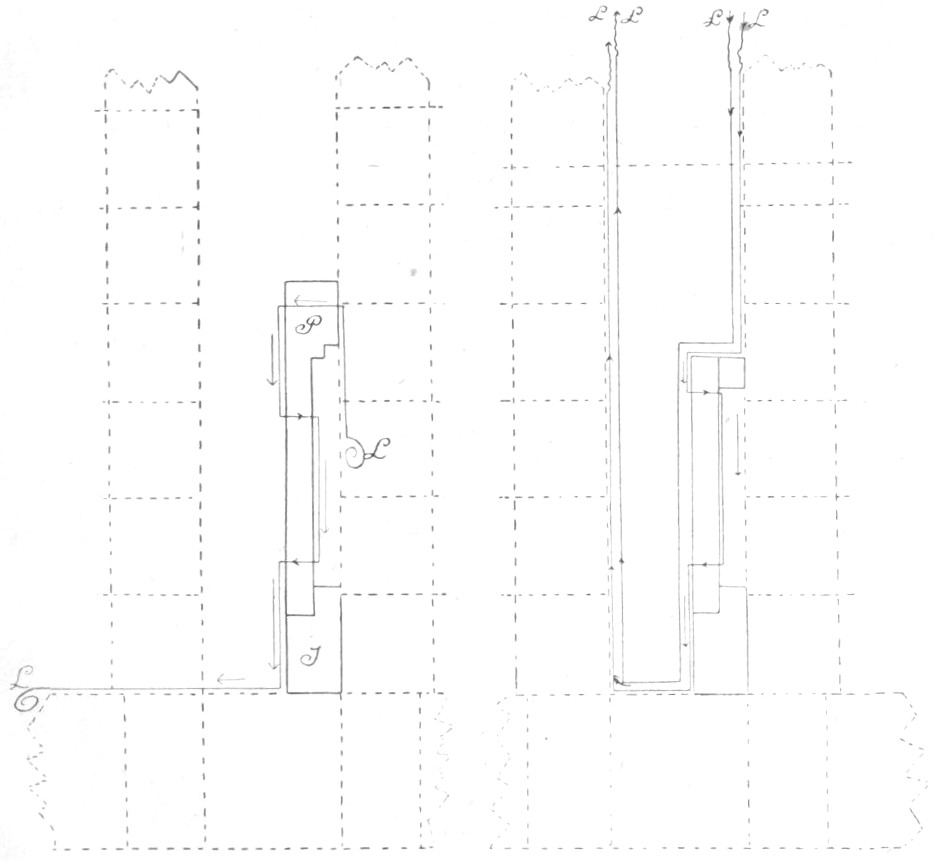
Dig. 31. Guide stitches.
Left figure: J - rule. P - headrest side board. L - wire threaded through P and wrapped at the ends. Folded side guiding stitch. Broken lines show a section of the workshop.
Right picture: L - Compound top guiding stitch. L - straight guiding stitch.
Warsaw Street 4
The described slats are an addition to the board, so instead of nailing them to the headrest, you can use appropriate legs, made of slats of the same cross-section and lightly nailed upright to the tops of the board. The board cannot be used instead of the described set of slats. because, by separating the top of the headboard from the inside of the workshop, it would hide the rows of holes intended for threading stitches.
We have finally set up the headboard, which causes us so much trouble, but before we start building the hive, we will check whether the vertical rows of holes intended for sewing on the headboard are made in the right places, i.e. whether they fall against the grooves crossing the workshop alleys and made on the plate, then whether they are made grooves in the headboard boards for the stitch needles between the holes, and finally we will proceed to designate space for yet another, this time temporary holes, to be used for pins.
15. Stitches. At the height of the board and the headboard, there are four levels of pinholes in the workshop posts, which are needed when pressing the straw opposite the headboard. In these places, the pins will go through additional holes in the headboard boards, which we will make opposite all the posts, on the side boards. like peaks. These holes do not belong to the set of triple holes in these boards, they are only for plugs. The triple holes are for threading the wire for the guide stitch and the twist stitch. The names of these stitches are given above on page 25. Sets of triple buttonholes should be placed on the headboard between the posts in the middle. There are three holes in each set: the middle one is for threading the wire into the guiding stitch, and the two side holes are for the twist stitch. In each section between the sides of the headrest, a vertical row of three sets of holes is formed. The first set is located on the foundation for the frames and the extension, and the next two on the side or on top of the headrest, on which there are not three but two sets of holes in vertical rows. Through all the center holes of the described sets, we thread the knitting needles for the compound stitch, and through the two side holes of each set, the wire for the twist stitch will be threaded.
We distinguish between straight and carabiner compound guiding stitches.
Cut pieces of wire 250 cm long for the guide stitch. We will wrap each individual wire halfway into a coil with a small cross-section. We will thread the other end of the wire through the foundation from the inside, then we will return with it through the next hole inside, and then through the next third hole we will go out; finally, the surplus end of the wire will be wrapped again in a coil as above. This is how we will pass all the gaps between the bars. Insert the wire from the side of the mat into the headrest to the gable boards and pull it out through the second hole. When this work is finished, there will be 14 pairs of wire balls in the workshop, half of which will hang inside the headboard and the other half outside the edge of the workshop. These are not all guiding stitches yet, these are more complex stitches, there will be one in the gaps between the posts of both sides of the hive and two in the gaps between the posts in the tops of the hive. In Figure 25 on the workshop plate, Compound stitches are drawn with a double wavy ruler (letter L).
There will be straight guide stitches regardless of the compound stitches; there are 8 of them, and in the drawing they are marked with a single wavy line (letter L). The straight guiding stitches differ from the previous ones in that they bypass the headrest boards, not going through the holes, but they guide the entire honeycomb wall mat with some inaccuracies, but the latter will be evened out with twist stitching. The illustrations in figure 31 highlight the difference between side fold guide stitches and top stitches, as well as straight stitches. Wire length as above.
While sewing the hive, we need to use one more type of guiding stitch, which we will call the guiding stitch. Its direction is shown by the wavy line M in the four corners of the workshop slab, intersecting the street in Fig. 25. The purpose of this elaboration is of the corners is to maintain the form of the corners of the hive and their special fastening. This stitch is no different from the one shown in Figure 16; it will not be prepared by us in advance, because neither the foil board nor the headboard box interfere, while the simple guiding stitches, encircling the entire walls across, must be prepared in the same way as the complex stitches and hung with rolls of wire before starting to lay the straw in in the streets of the workshop, to the number of pairs of glomeruli (tangles) described above, there will be eight more, loosely hung in the right places. So let's count: eight straight ready stitches, fourteen compound stitches, twenty-two in total, plus four unprepared corner stitches, which we will tighten only after pressing the straw to the entire height of the workshop, 26 in total.
There are quite a lot of stitches in the beehive, but it will not take much more than a day to sew it, and the wire will cover the entire hive not much more than 100 meters, so the construction cost comes down to almost pennies. Already after sewing a few hives, the cheapness of construction will cover the outlay spent on the rule and in a short time will reward the science.
We have one difficulty. to a solution that we have not taken into account so far, namely: how to compress the straw on the corners of the hive.” In the descriptions of other authors dealing with the sewing of straw hives, slats-tables are prescribed. cut diagonally at the edges, entering shallow diagonal frames made on the posts: each outer corner on two sides and each next to it on one side. These slats, 100 mm high, serve as pledges and prevent the straw, bent at the corners, from leaning out beyond the line. As the work progresses, the slat is moved up to the end of the height of the board. In our case, we will use the rebating of the corner and side posts, but we will have difficulty with the metal sheet with which we cover some of the posts, as discussed above: So, the metal sheet should be tapped into the rebates, prepared in advance. However, we will cut the ends of the mats with greater care, as little as possible injuring the edge of the sheet, at which the rebate begins. For each corner, we need two planks of pledge, so we will make eight in total.
Finally, we proceed to the laying and compression of the straw:
The best straw for sewing beehives is rye straw, not too short, but relatively fine and clean, without weeds. It must not bristle too much or break during the work, so it must be sprinkled with water the day before: but it must not be wet, so that the wire does not immediately rust.
Some masters of sewing straw hives "board" the outer sides with reed blades, cleaned of sheaths and trimmed to the correct length. This not only looks nice, but is useful, for the reed gives the hive beauty and durability: but I do not advise a beginner to try the record until he has learned how to make hives with nothing but straw.
We put the straw around in one direction, starting from the knowie, but spreading the thicker ends of the straw slightly along. The wall must be uniform without bumps and hardenings, which a skilled hand will feel immediately when pressing the lever.
In the bends of the streets, i.e. at the corners of the hive, the straw is bent, carefully paying attention to care and not sparing fingers and methods when pressing the corners. An additional piece of board will be useful here, which will be discussed in a moment when compressing the part of the walls opposite the headboard. Our lever will not reach the corners of the alleys, despite the cross-shaped extensions of the central opening, intended for moving the movable post. I don't think about how to move the pins, because I described this detail on page 25.
The compression of the straw at the height of the foil and the headrest can be done manually. If manual compression is difficult, a lever can be used, but then a log of appropriate width and thickness (60 mm) should be placed under it. We will not describe the dimension of the balika, everyone who encounters difficulties will introduce this improvement for themselves and it will be very easy to find the dimensions.
Next, we place straw in the lanes to a height of 345 mm. i.e. to the sixth hole on the red side of the moving post. Then we leave the pins plugged in one of the gables, and from now on we will not put straw there, leaving an opening for the valve door. We are not discouraged by the fact that at the top above the valve, the end of the work is higher than the level of normal holes around the workshop: after plugging the fifth holes around, we add straw starting from the top, after pressing it, we move the pins to the Z mark, then put the straw around and thread the normal sixth holes. Further holes in this stitching are not active until the end of the work. In the second peak, where we do not leave a hole. the sixth holes are omitted.
Finally to the end, i.e. up to a height of 810 mm. we lay without obstacles, taking into account the outlets, but from the side of the valve, the ends of the straw come out of the streets A and E (Figure 25) straight outside and will be cut at the posts 1 and 9: 17 and 25 on their right to a depth of 465 mm, i.e. to the last Z plugs left in the top. When finishing cutting, be careful not to cut a single straw below the top plugs. The height of the opening left for the door-valve consists of the height of the valve 370 mm and the thickness of the bottom 95 mm.
Between the posts 4 and 12: 5 and 13 we put outlets. The first upper outlet should be placed at a height of 465 mm (250 mm from the ceiling, 165 mm height and 50 mm foil), counting from the panel surface: on the side of the movable post. From the outside of the board, the height will be greater, because the outlet is sloping. The letters K in Figure 26 indicate the location of the outlets. We will place the second outlet (lower) so that its lower edge (upper for now) comes out from the floor level, i.e. lower than the last plug (letter S) by 95 mm. It should be noted that the inclination of the outlets should fall downwards only after removing the hive from the board, currently it should be turned upwards on the board.
Straw hive outlets should have the same opening as described above. i.e. 9 mm and 120 mm wide; they are slanting boxes without a bottom. The outlet to the straw hive is made of a piece of a half-box 95 mm wide and 150 mm long. We wipe this piece of board obliquely along, but not from corner to corner, we will only step away from them a bit, and we have to hit the right inclination as in the above-mentioned drawing. Sawn pieces separated by 2 slats 9 mm high, 120 mm apart. In order to protect the outlet-boxes from slipping out of the mat, small nails sticking up and down are inserted into the ends of the boxes.
When we finally get to the last stopper holes, we proceed to finish the guiding stitches. We unwind individual pairs of coils-glomeruli one after the other, strongly close the circle of guiding seam, then we thread the longer end of the wire into the needle and sew it with a twist stitch. When our wire runs out, we piece it with a fresh piece, measuring about 2 meters, and when connecting, we make sure that the ends of the knot do not stick out against the wire pull, but point to the back of the pull. In order to avoid protruding these ends, we make them a little longer outside the knot, so that after making the stitch, the ends can be folded and pressed into the wall.
One of the folded guiding stitches divides the opening in half. To avoid this, we bypass the outlets with sticks stuck in the wall: the first one above the center of the upper outlet, the second and third on the side of both outlets, and the fourth one under the lower outlet. We pull the wire tightly both at the front of the wall and at the back. Then we cut a piece of wire about 50 cm for an additional stitch, we tie its end to the guiding stitch, just above the first peg, we plug two pegs on the other side of the outlet, already behind the posts (the same should have been done there), we lean the additional wire on them, we thread them again under post and tie under the outlets with the main wire of the Guide stitch. The sticks remain until we sew this stitch with a twist stitch, making sure that the latter presses both joints of the main stitch with the additional stitch and the places of bends near the pins into the wall.
By omitting the outlets, we left the part of the wall between them outside the stitch. You can use a regular guiding stitch with a twist stitch. In the middle, under the upper outlet and over the lower one, we pass the wire, tightening it after guiding it, then we sew it with a normal twist stitch.
Join the guiding corner stitches with a twist stitch, stitching the nearest straight guiding stitch with it from time to time, in order to avoid loosening and slipping of the entire stitch. When we sew the entire hive together, we pry it up to a height of 95 mm above the top of the posts. Now we insert the bottom, prepared in advance, paying attention to its even position, avoiding gaps in the hollow top with light blows with a wooden hammer on the free ends of the bottom, from the side of the valve, and then we sew the bottom with the sides of the hive using a circular stitch.
The joint of the bottom is exposed to the weight of the trunk, so it is possible to twist the hive during transport; so, regardless of the stitching, we will additionally fasten the bottom with wooden pins about 200 mm long, with heads and planed here and there along their length into cuts, similar to the teeth of a fishbone. The pins are threaded through the wall across the bottom.
The walls of the hive are strengthened in a similar way from the bottom up to the foundation of the frames, i.e. up to a height of 600 mm. The thickness of the pins does not matter, thinner ones are better, but they are woven more densely.
16. Finishing. So we have the whole sewn hive with the bottom. Now we remove it from the board, pushing it from the bottom evenly from all sides, it is advisable to be patient so as not to damage the board and the removed hive.
After removing the hive from the workshop, it must be charred with a bunch of simple straw, but not very much, because the point is to remove the protruding sheaths of straw, but at the same time to avoid turning the walls brown. We do the same with mats. which will enter the whole hive.
The holes in the headboard boards have already done their job. we glue them with varnish putty, used for windows, and fix the putty in the holes, covering the entire headboard from the inside with the same putty, thinly spread in the varnish. Sealing the holes is to protect the bees from pests, and the wire from rusting too quickly. In a similar way, we can paint the entire hive inside and out with the addition of a little paint.
Then we attach the valve. First of all, it must be fitted tightly so that it enters with some resistance, but so that it does not make too much noise when opening. Instead of a hinge, sew one side of the valve mat loosely in two places to the corresponding side of the hive (from the outlet side). Closing the valve can be done with a loop sewn from the same wire that we used to sew the hive into the other side of the valve, twisted and bent into a hook. At the end of the wall of the hive we stick a rather long test tube, made of thicker wire, the ends of which are bent backwards, the test tube is pushed into one of the twisted seams and the ends of the test tube are tried to be hooked to it.
On top comes the mat-cover, which we sew loosely from the outlet side to the upper edge of the wall in the same way as the valve door. Similarly to the valve, we use a bent hook or two hooks on the back wall of the hive. They will pin and press the mat tightly to the top edge of the hive so that it will open like the lid of a chest. In order to avoid problems with age, we will use an appropriate support for the time of work in the hive, with the help of which we will protect ourselves from falling down during work. We sew the support with a small hole at the lower end to the back wall in the fold under the cover, and rest the other end on the wooden headboard.
The bridges are attached to the outlet boxes, and the outlets are equipped with latches.
17. Visor. A hive built in this way can be placed on a stool made of battens or boards arranged on pins, it will be sufficiently durable and can be used under the blade without additional devices. For the entire hive, which is to stand on a wheel, a roof is needed, as we already know, which is a separate structure. In the apiaries. for crops and those in which the trunks overwinter in lockers, the roofs should be made of two separate mats joined together with hooks. These are foldable canopies, they do not take up much space on the road and storage. they are quite durable, but if the mats are not joined properly, they can leak; Besides, they have the undeniable advantage of cheapness, especially when they are sewn not with wire, but with reed bast or strips of roots, which adds durability. The thickness of the mats for the canopies is 50 mm. They can be made in a workshop designed for sewing straw hives, provided that not too difficult or expensive additional devices are used.
If you intend to sew mats from the beginning in the workshop described above, you should lengthen the board in both directions by 125 mm, i.e. by 250 mm in total. The extension may not cover the whole width, because we only need to extend one street. so it is enough to lengthen it by half the width of the slab. On the additional surfaces elongated on both sides, we will place two more pairs of posts, extending the street A, fig. 25 by 250mm. In this case, the street between the peripheral pairs of posts will have a narrowed width. namely 50 mm.. and roof mats will be cut to the right of the additional posts. The width of the alley A, for the time of sewing roof mats, should also be reduced to 50 mm by adding, between each pair of posts. pine slats of the same height as the posts, (counting from the level of the board) 45 mm thick, fitted with holes corresponding to the holes of the oak posts and fixed in the alley with wooden pegs. The pegs are driven into the three upper holes of the slats permanently, and the protruding ends are pushed into the holes of the oak posts as needed. Needless to say, the front additional oak post, both to the left and right of the normal posts, should be positioned in line with these posts (25 - 32), and the rear additional posts (17a and 24a), intended to form an alley width of 50 mm, will approximate the The front ones will meet the row of posts 17-24 by 45 mm.
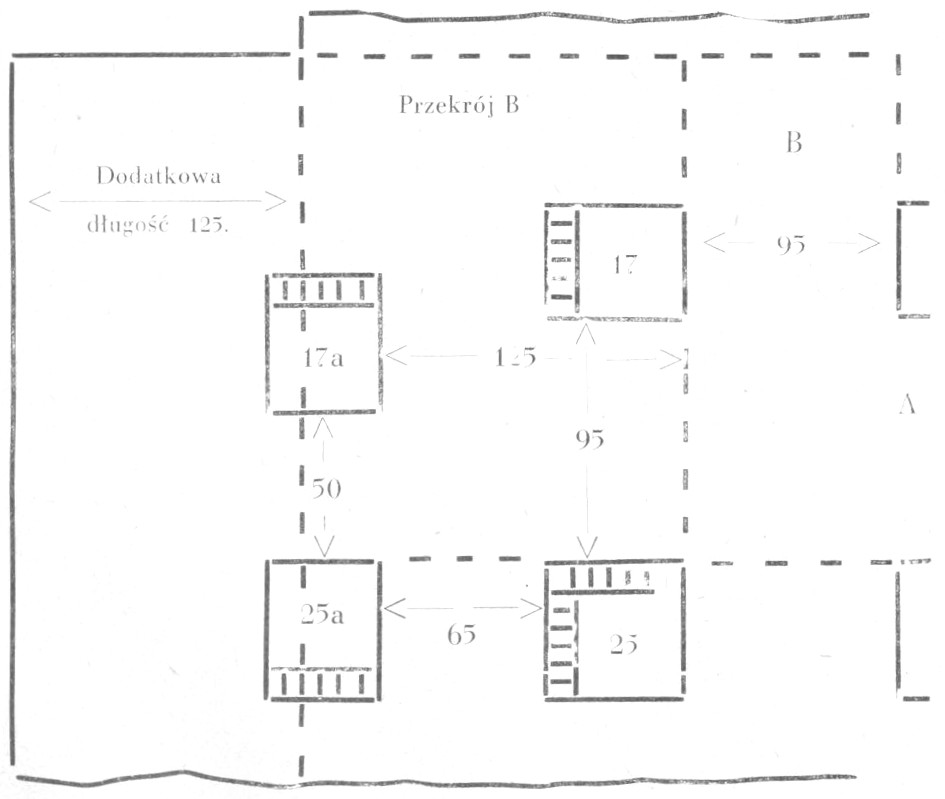
Dig. 32. Additional device for sewing canopy mats. Left side.
Let's call the pairs of extra posts on the left the numbers 17a and 25a and on the right side of the workbench 24a, 32a. The posts will be made, perforated and inserted similarly to the normal posts, as mentioned above. Their distance from the side posts is 65 mm and they will be covered with zinc sheet from the inside on the right side of the additional posts 17a, 25a, on the left side of the posts 24a, 32a, here we will cut the straw after sewing the mats. (Fig. 32).
Roof mats need to be pressed as hard as possible, they can be made of slightly damp straw, but after sewing they are thoroughly dried in the sun, but we will sew them together, not pressing very hard. The changed method of sewing roof mats is to lead to proper compactness while avoiding stains in the places where the sip exits. The wire is not suitable for sewing canopy mats, because under the action of atmospheric moisture, it not only deteriorates itself, but also quickly causes rust to eat straw.
Stand-alone, completely straw mats are suitable for roofs, rather than framed or sewn into wooden frames: non-uniformity of the material accelerates the rotting of straw and wood, thus increasing the initial cost of production, and does not contribute to greater durability and strength. It must be admitted that the mats for the canopies in our project will also not excel in excessive durability, but there is no advice for those who want to use the most affordable and cheapest building material.
Our mats have an additional disadvantage, namely, sewn crosswise and placed in the hives in this way, they will retain water, which will accelerate rotting, but in our workshop, we cannot sew in a different direction of straw, so it would be necessary to build a new, less expensive pine one. but enough. An additional description of such a workshop would exceed the scope of this booklet, and it is not necessary, because each of the beekeepers who builds the rule described above will surely be able to tinker the simple workshop in question. The cost of the workshop for sewing canopy mats will not be too great. The work of mats requires diligence in execution, like any decent job, but we will focus our attention not so much on the accuracy of dimensions as on the cohesiveness and waterproofness of the mats. Hence the conclusion that in the absence of oak, we will use dry pine material. The top can be made of 50 mm logs and the posts will measure 50 X 60 mm in cross-section. The height of the workshop should be equal to the width of the roof, i.e. 1200 mm, and the length is 900 mm, i.e. twice the height of the roof panels, and the posts are to be spaced so that the mat can be cut into two unequal parts after sewing: The higher mat will measure 500 and the lower 400 mm in height. (Fig. 33).
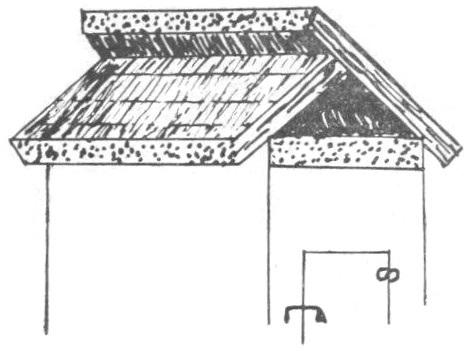
Dig. 33
Roof made of straw mats, foldable.
Another non-folding roof is made of 25X25 mm inch battens. We will use one 1200 mm batten for the ceiling, two for the parallel lower ones. 1200 mm each, for the gable rafters of four 450 mm each and for the top wall plates of two laths 570 to 580 mm each. All connections are made in half claws (according to Kuśmierski: cross overlay joint or cross notch), whereby the connections of the ceiling and eaves panels will be straight crosswise, and the connections of rafter battens and wall lath locks will be diagonal crosswise.
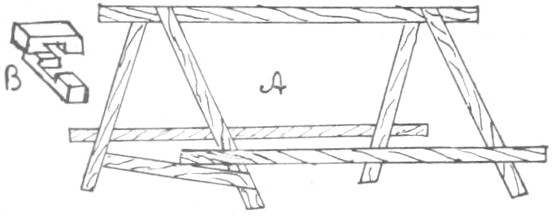
Dig. 34.
A – structure of the non-folding canopy, made of battens. B - Straight cross overlay joint, used when connecting rafters with ceiling and eaves battens.
Our canopy, rectangular in the ceiling, measures 1200 mm in length. the height of the sides is 420 to 430 mm and lies on the cover of the hive on two gable patches, whose connections with the rafters should fall out in such a way that the latter rest against the edges of the mat covering the hive. Therefore, the wall plates will support the roof, and the rafters will not allow it to slide around the hive during strong winds. Figure 34 shows the entire structure of the canopy.
The described structure of the canopy is hewn as follows: first, we lay the straw in thin layers, alternately with a fairly thick layer on both sides, then arrange the ceiling with a wolf (fig. 7 letter N). made of two thin slats, nailed to the ceiling batten and rafters through straw with nails. Cut the surplus length of straw along the same line with the ends of the rafters and nail the straw to the eaves battens through the split halves of the hazel rods.
Using the removable visors is very simple. The roof made of mats can be folded and leaned against the dead top of the hive, the non-folding roof is grabbed by the top wall plates and placed on the ground in the usual position at the ends of the rafter battens, or placed on the top, i.e. at the ends of the ceiling and eaves battens. Some people set their roofs on a trestle built in the form of a cross, moved during beekeeping work from hive to hive. The trestle can be a useful help, because it allows you to save the cover and at the same time serves as a handy storage for beekeeping tools, because it may be staring at a small box in the form of an elongated drawer.
THE END.
LIST OF ITEMS.
Preface to the second edition
ul
1. Conditions of a good hive
2. Warsaw street
Frame
Bottom. walls. Door-valve
extension
Extension frame
Beehive boarding
Outlets, latches
Peak
3. Hive supplies
Barrier grille
Pillow
Straw mats
4. How to redo Lewicki Street
5. Changes in the Warsaw hive. superstructure
6. Material for hives
7. Painting the hives
8. Cheap Warsaw high street
Warsaw straw beehive
9. Overview
10. Rule
11. Preliminary preparations
12. Headrest
13. Rule
14. Construction of the hive
15. Stitches
16. Finishing
17. Visor
Foldable canopy made of mats
Non-folding visor